2 miljoen vaccins per dag
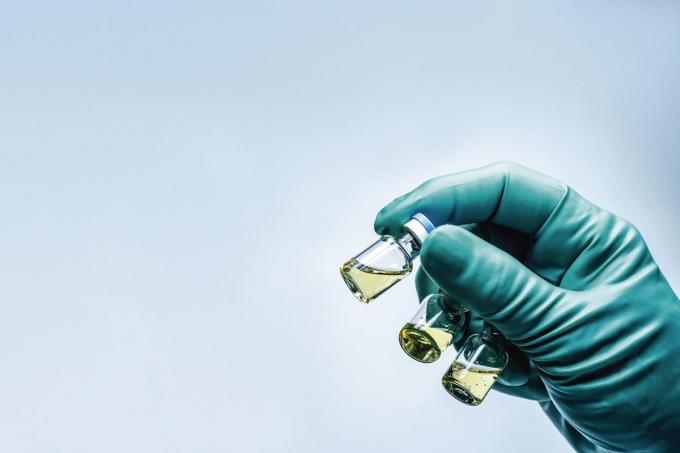
Het coronavaccin was in minder dan een jaar klaar. We zouden haast vergeten hoe complex het hele ontwikkelingsproces is. De productie van het recentste product van GSK – een zonavaccin, en dus geen coronavaccin – toont hoe fragiel het kweken van een biologisch vaccin is. Trends mag exclusief meekijken.
Sinds de coronacrisis weet iedereen dat België een hoofdrol speelt in de ontwikkeling en de productie van coronavaccins. Onze farmavallei draait op volle toeren dankzij het gunstige innovatiekader dat de overheid heeft gecreëerd, onze centrale ligging in Europa en de sterke verwevenheid van universiteiten, ziekenhuizen en bedrijven. België biedt plaats aan ‘s werelds grootste productiecentrum voor vaccins. Tussen de velden van Waver produceert GlaxoSmithKline (GSK) de adjuvant voor drie kandidaat-coronavaccins en een dertigtal andere vaccins.
Er werken 9000 medewerkers van 80 nationaliteiten bij GSK België, een onderdeel van de Britse farmagroep. Op de historische site in Rixensart wordt aan onderzoek gedaan. De ontwikkeling met preklinische en klinische testfases en talrijke controlemomenten neemt gemakkelijk veertien jaar in beslag. Een deel van de productiesite en het administratieve hoofdkwartier verhuisde eind jaren negentig naar Waver. Vanuit het globale productienetwerk vertrekken meer dan 2 miljoen vaccins per dag naar 162 landen ter wereld. In 2020 werden 580 miljoen dosissen verdeeld. De prijzen worden berekend worden volgens de financiële draagkracht van het land. De roots van GSK lopen terug tot de Leuvense hoogleraar en rector Piet De Somer. Hij ontwikkelde en produceerde in de jaren veertig een van de eerste poliovaccins. Via verschillende fusies groeide GSK uit tot de farmagroep van vandaag.
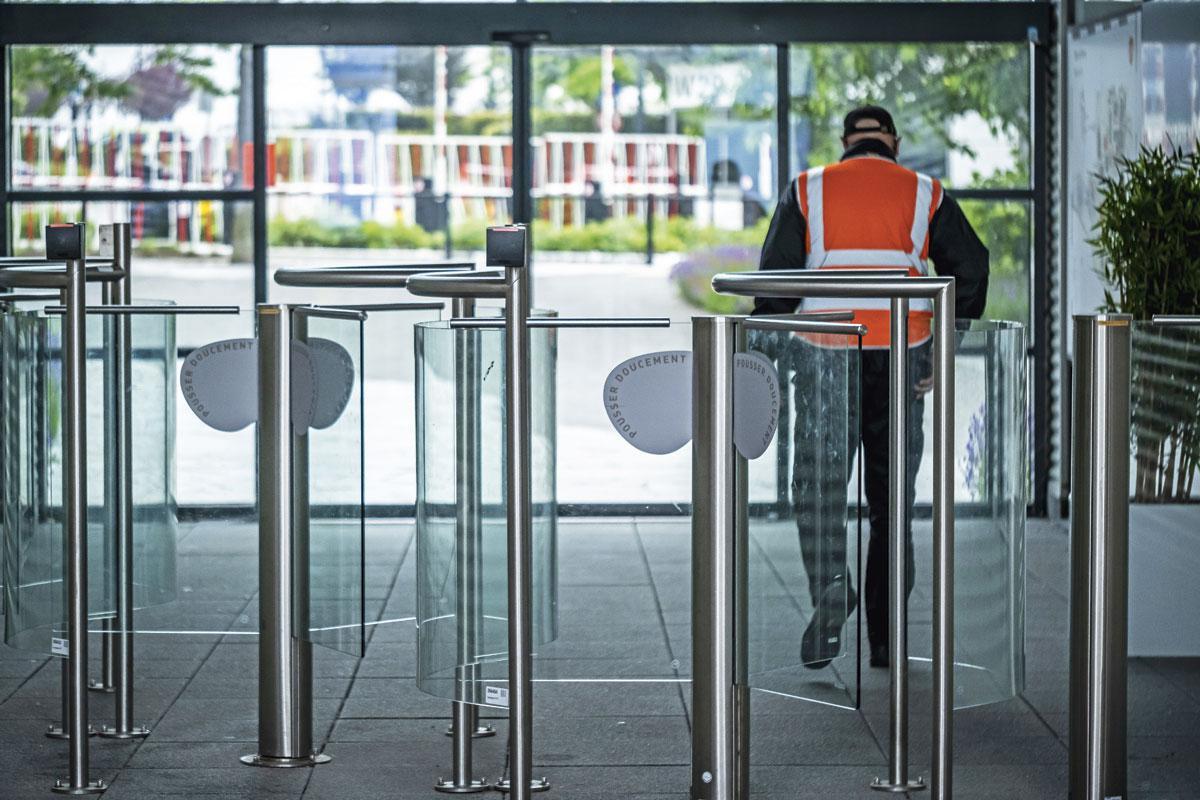
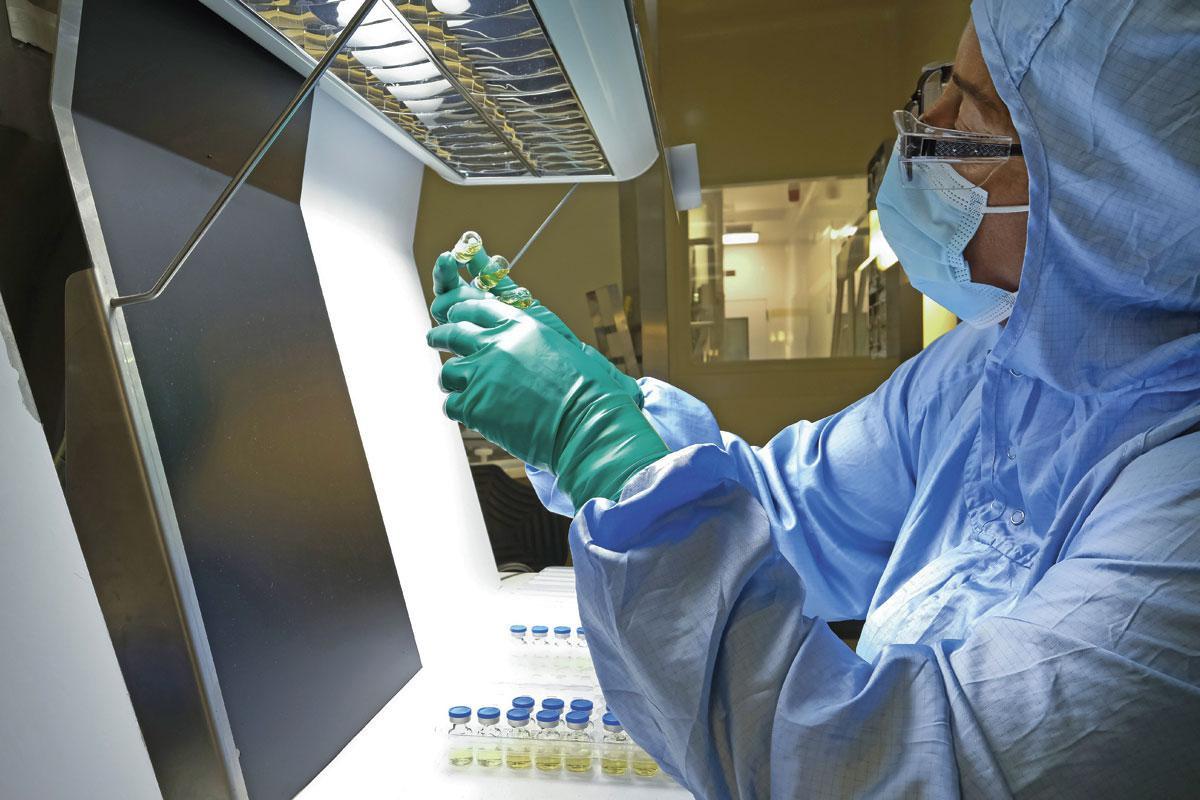
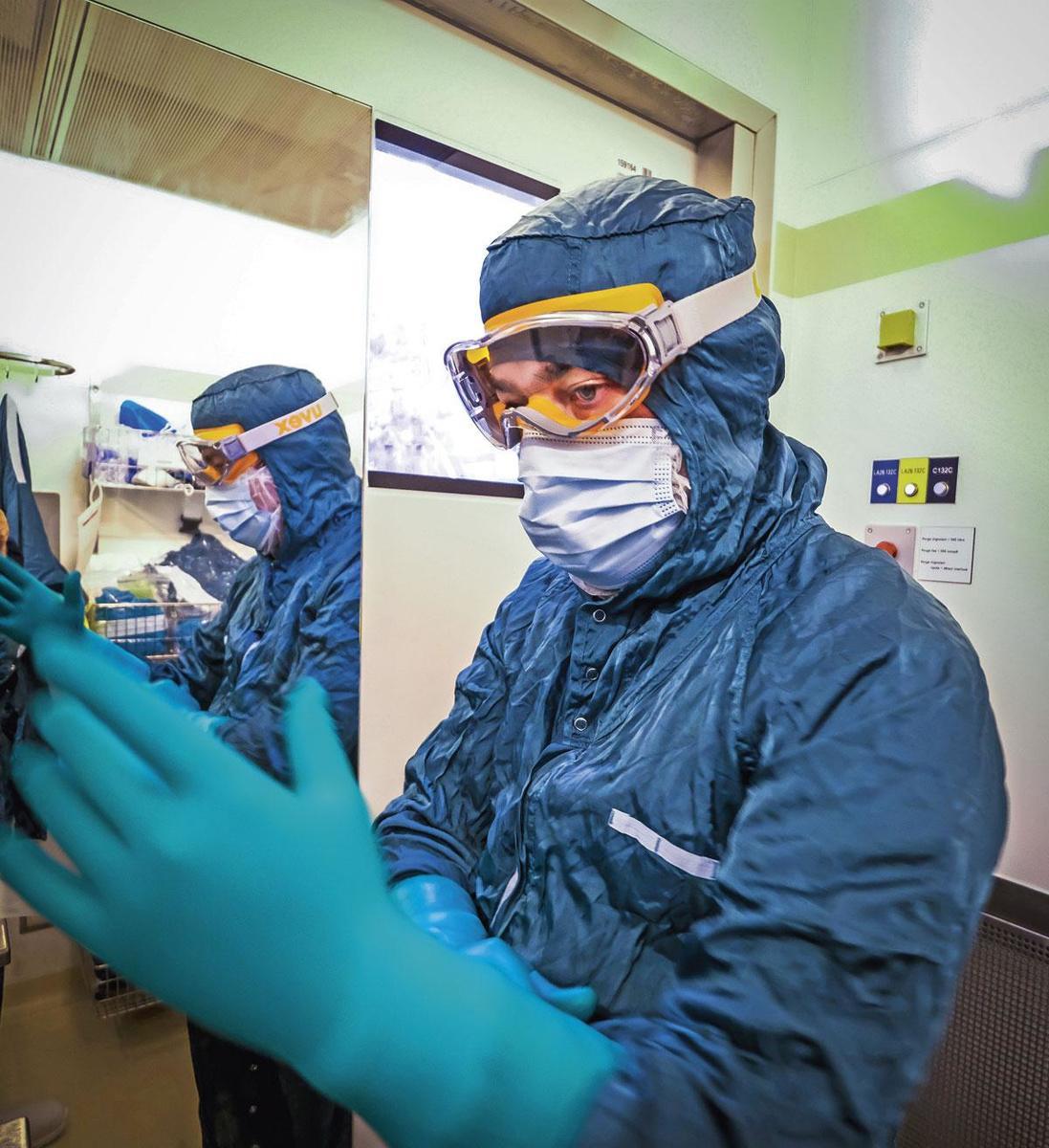
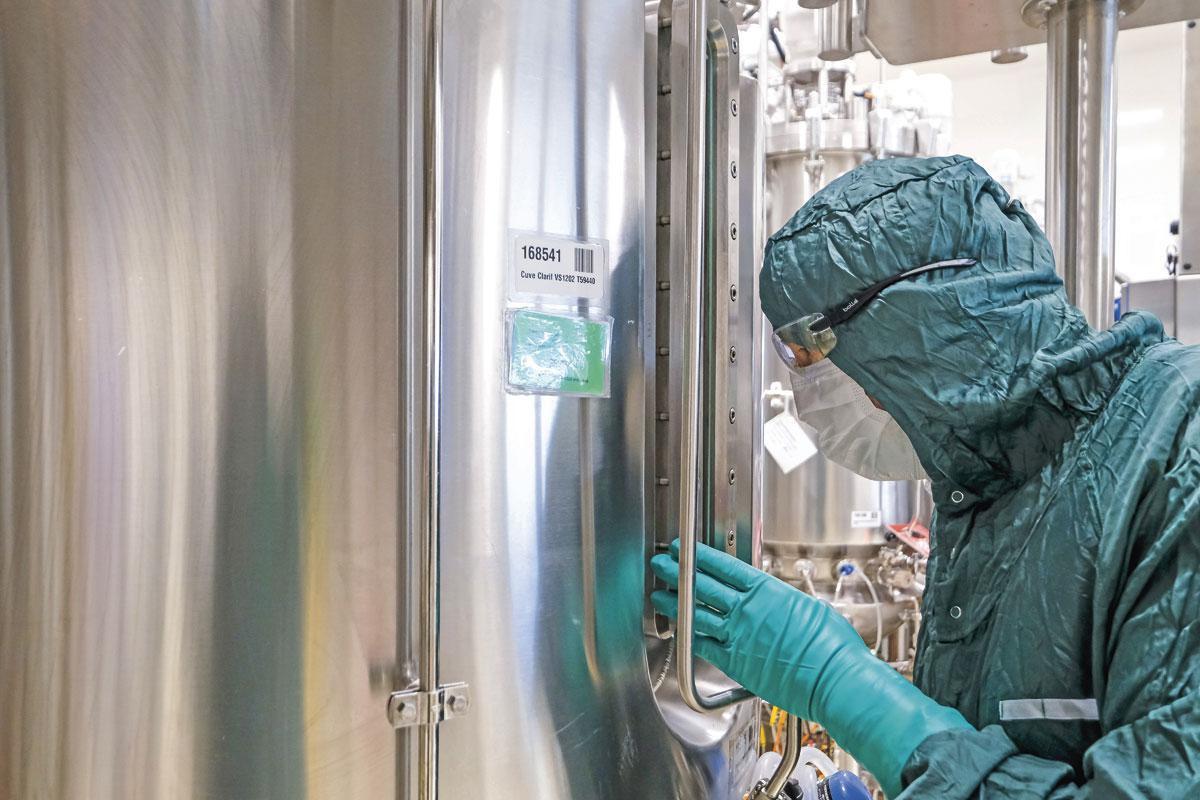
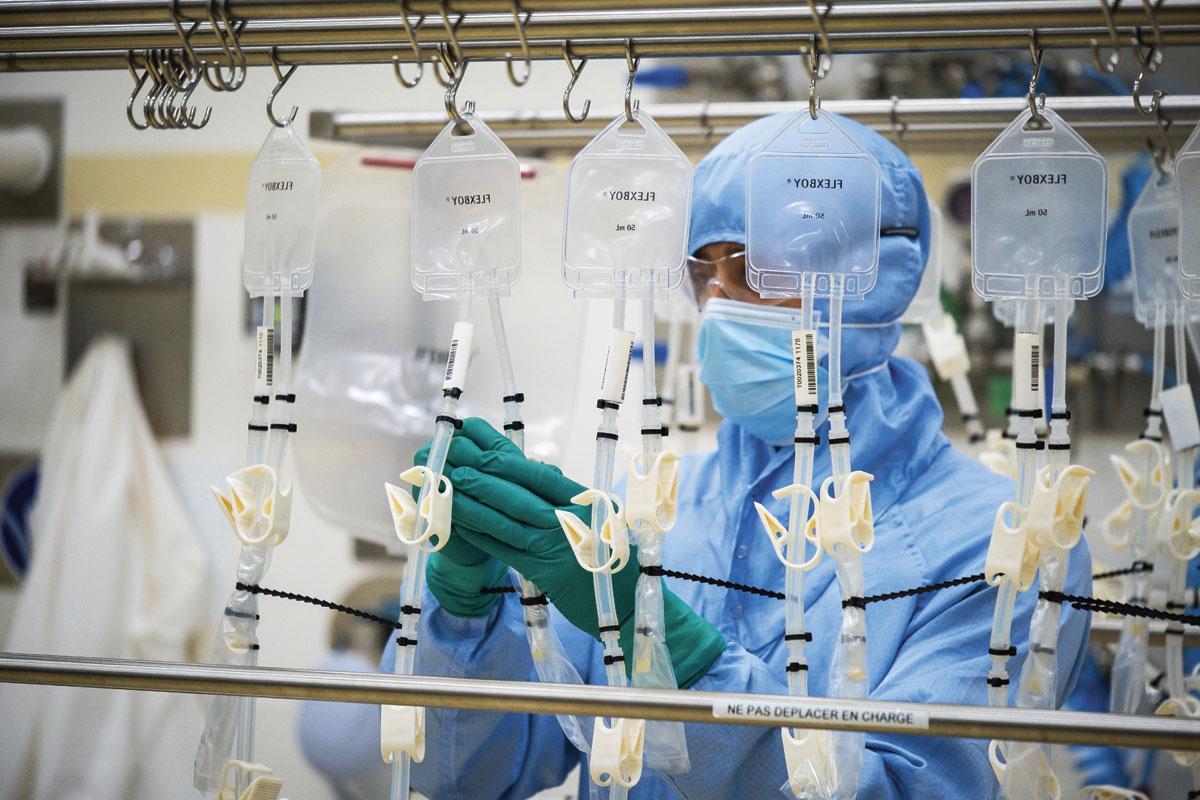
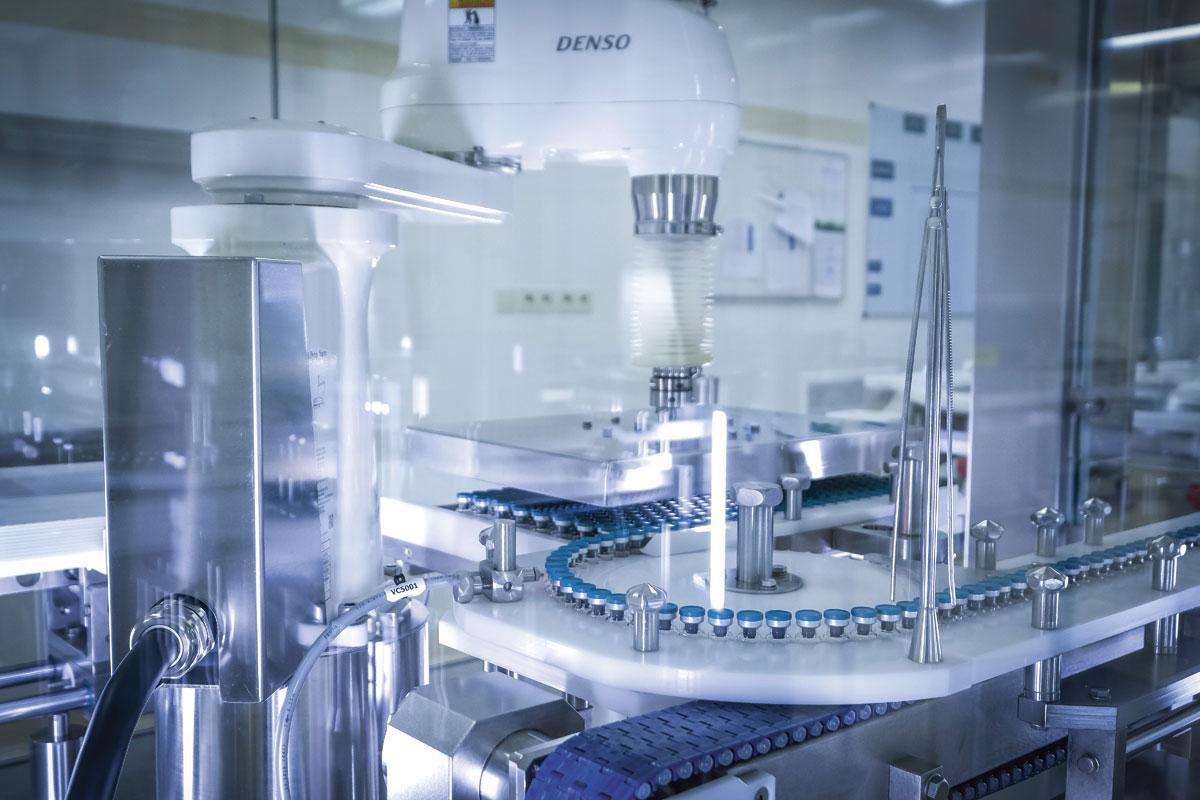
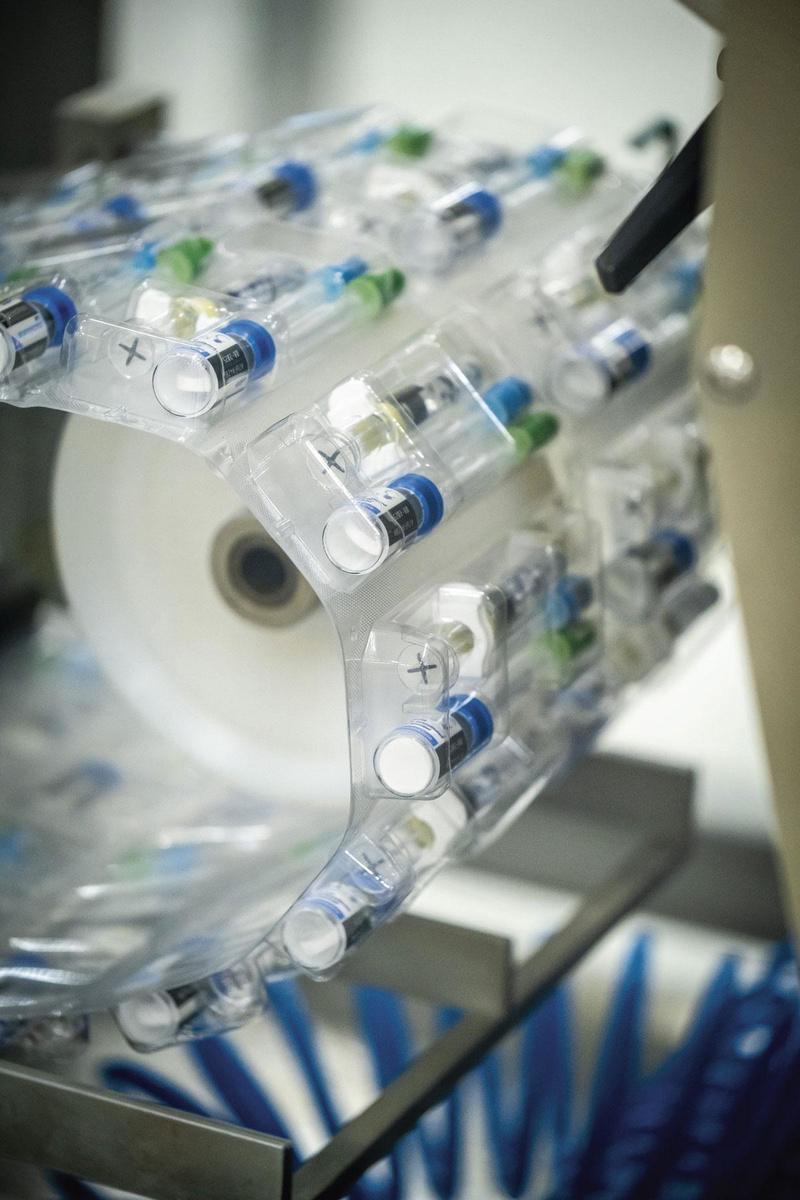
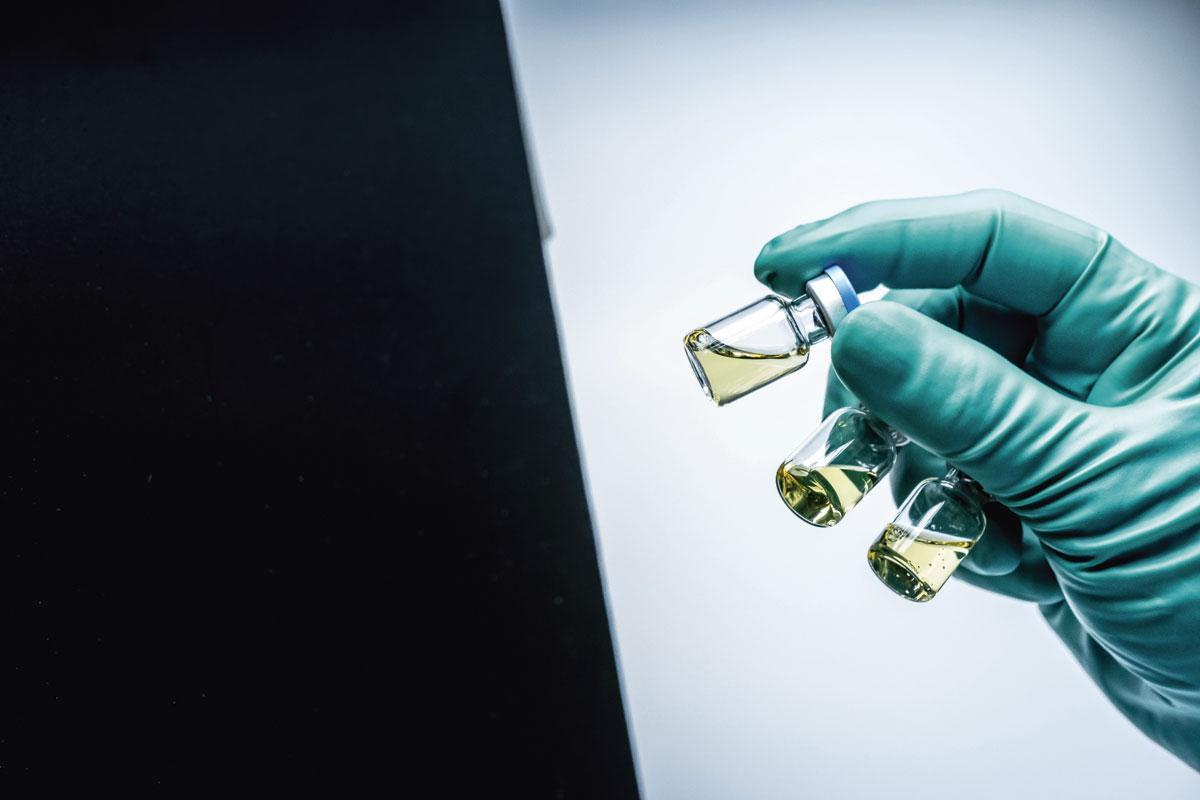
Fout opgemerkt of meer nieuws? Meld het hier