De producent van spades Polet-De Pypere kan bogen op meer dan anderhalve eeuw vakmanschap. De ambachtelijke knowhow is inmiddels geïntegreerd in een hoogtechnologisch productieproces.
In de negentiende eeuw vond je nog in bijna elk Vlaams dorp een smidse. Boeren en landarbeiders lieten er hun handgereedschap smeden. Door de industrialisering kwam het ambacht onder druk te staan. De dorpssmidsen verdwenen of ontpopten zich tot kleine fabriekjes. Dat laatste gebeurde onder meer met de smidsen De Pypere in het West-Vlaamse Ardooie en Polet in het Oost-Vlaamse Borsbeke. In 1998 kwam De Pypere in handen van de familie Devos. In 2015 volgde een fusie van De Pypere en Polet, waarbij ook de familie Ampe in het kapitaal stapte. Het fusiebedrijf is vandaag een onderdeel van de familieholding Icarus Invest, die onder meer ook de eigenaar is van enkele metaalverwerkende bedrijven zoals Metafox, Maes Metal en Dafco.
Sinds 2019 zitten de voormalige concurrenten samen in een nieuw bedrijfspand van 8.000 vierkante meter in Ardooie. Jaarlijks worden er naast 250.000 schoppen en 60.000 spades nog tal van andere handgereedschappen gefabriceerd. De productcatalogus omvat 3.000 artikels. De fusie was vooral nodig om voldoende schaal te creëren en het productieproces grotendeels te kunnen automatiseren. De twee merken blijven naast elkaar bestaan, benadrukt medezaakvoerder Xavier Devos: “Het gereedschap van De Pypere heeft andere kenmerken dan dat van Polet. Beide merken hebben ook hun fans. Als adidas en Nike ooit zouden fuseren, zullen ze ook niet een van die twee merknamen afschaffen.” Er werken 65 mensen voor Polet-De Pypere, van wie ongeveer de helft in de productie en de assemblage. Voor 2024 verwacht het bedrijf een omzetgroei van 5 procent tot 16,3 miljoen euro.
1/ Vormsnijden en aanslijpen
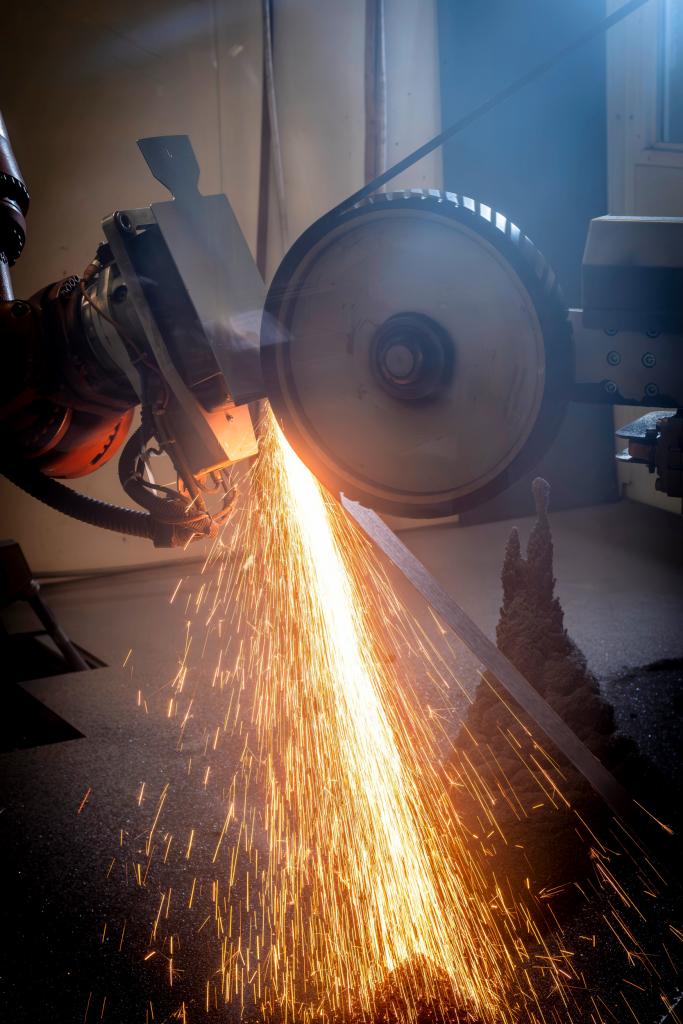
Naargelang de toepassing verschilt het spadeblad in vorm en afmeting. Uit een vlakke staalplaat snijdt een laser de gewenste vorm. “Vroeger deden we dat met een stansmachine”, zegt commercieel directeur Stijn Temmerman. “Maar een lasersnijder biedt meer flexibiliteit. We kunnen kleinere volumes uitsnijden en makkelijker kleine aanpassingen aanbrengen.” Polet-De Pypere gebruikt een eigen staallegering. “Het is belangrijk een goed evenwicht te vinden tussen hardheid en taaiheid”, benadrukt Temmerman. Onder aan het spadeblad wordt in een slijpinstallatie nog een scherpe snede aangeslepen.
2/ Opwarmen, buigen en harden
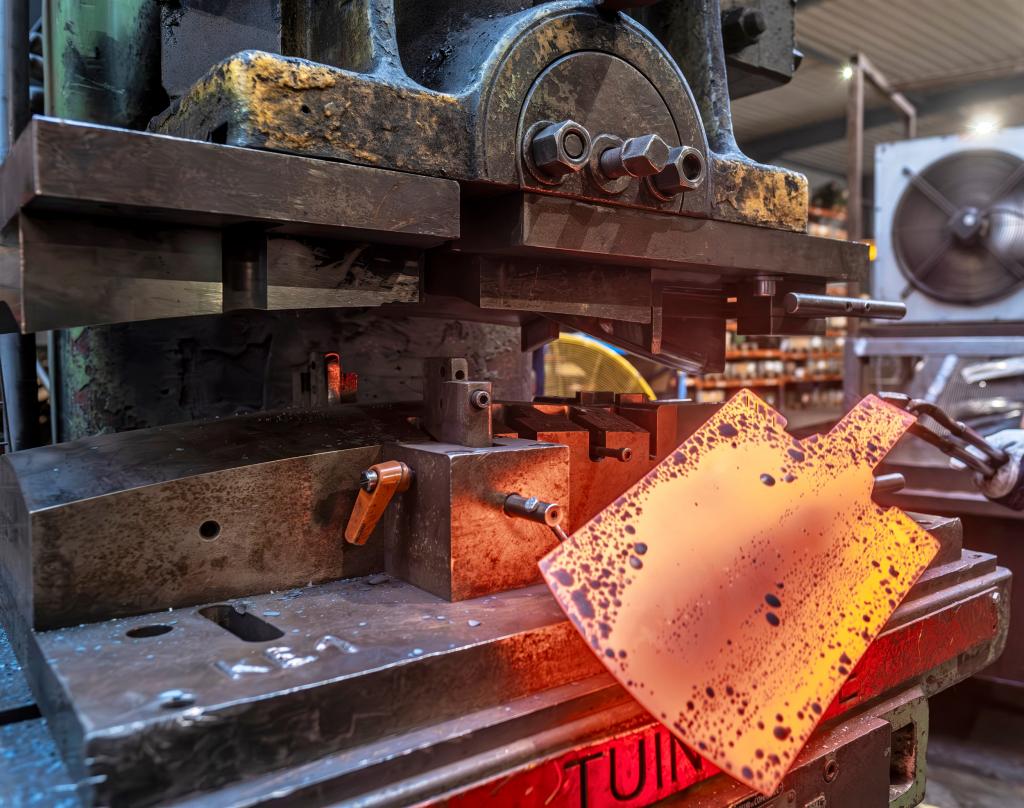
Om het spadeblad zijn buigvorm te geven moet het opgewarmd worden. Een robot legt de platte spadebladen op een kettingband die door een oven met een temperatuur van 950 graden Celsius trekt. Aan de andere kant van de kettingband haalt een operator de verhitte spadebladen uit de oven en legt ze in een hydraulische pers, waardoor ze hun buigvorm krijgen. Vervolgens dompelt de operator de spadebladen onder in een vloeistofbad. “Dat creëert een schrikreactie die nodig is voor het harden van het spadeblad”, legt Stijn Temmerman uit. “Klassiek gebeurde dat in een oliebad. Maar dat is een vervuilend proces en het houdt ook een risico op brandgevaar in. Daarom opteren wij voor een waterbad met een polymeer dat de eigenschappen van olie nabootst.”
3/ Oplassen van de spadeleest
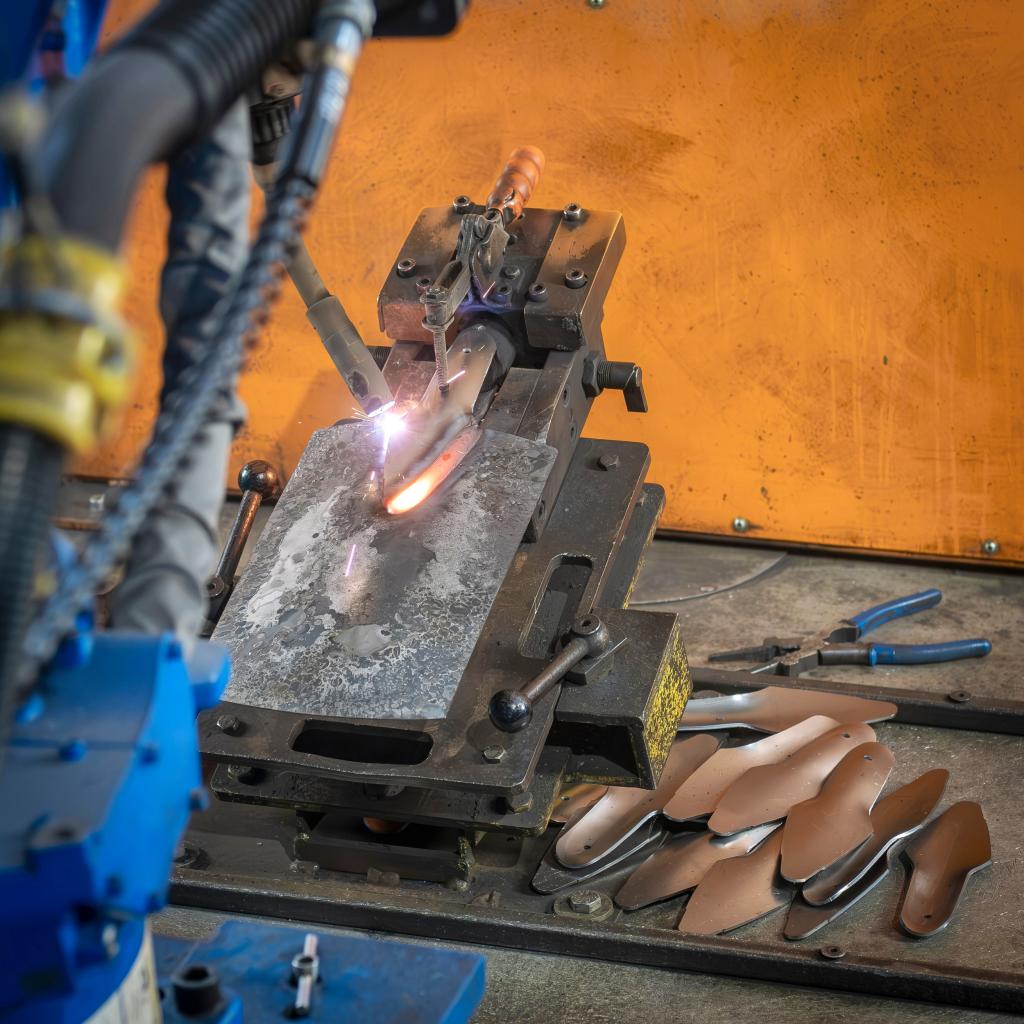
Op de inmiddels geharde spardevorm wordt vervolgens een leest gelegd. De leest is een verbindingsstuk in staal tussen het spadeblad en de steel. Een lasrobot last de leest op het spadeblad. Leest en spadeblad moeten finaal een stevig geheel vormen.
4/ Slijpen, staalstralen en polijsten
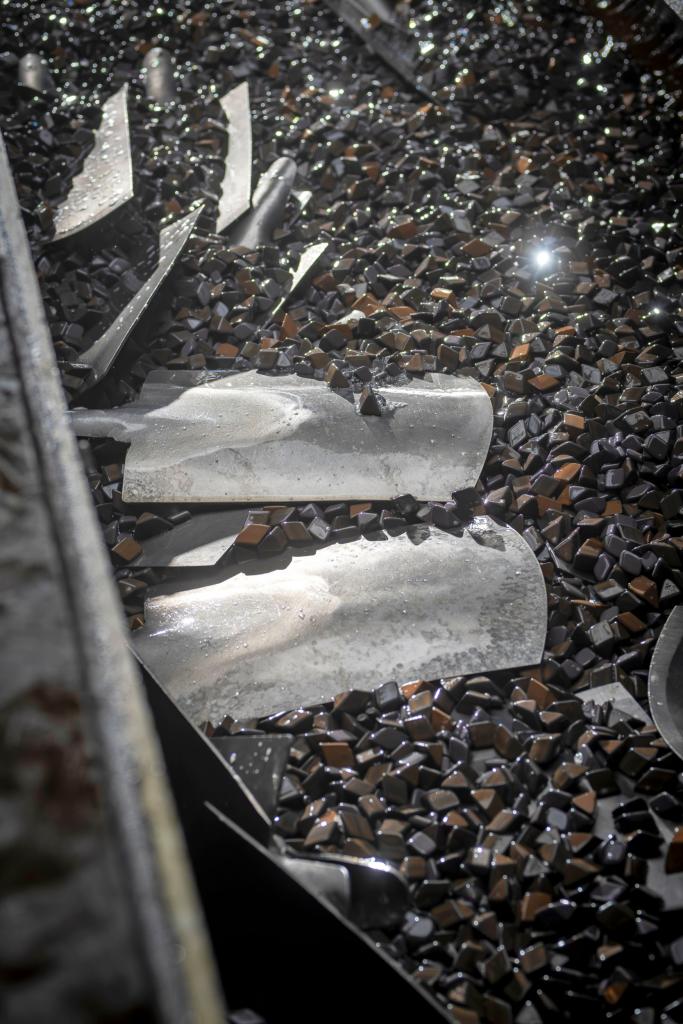
Oneffenheden die ontstaan bij het lasproces worden met een slijprobot weggewerkt. Na het slijpen wacht de spadebladen een straalbehandeling. Een machine blaast onder hoge druk kleine staalkorreltjes tegen het oppervlak van de spade. Dat proces verwijdert de oxidatielaag die ontstaat bij het harden. Daarna verhuizen de spadebladen naar de polijstmachine. “Een gigantische machine van 20 ton die gevuld is met 6 ton keramische stenen”, vertelt Temmerman. “Die machine laat via een schudbeweging de keramische stenen op de spadebladen slaan. Onze beste spades en schoppen zitten tot meer dan twee uur in die machine. Met als resultaat dat je een heel glad en krasbestendig oppervlak krijgt. En dat verhindert dat er aarde aan het spadeblad gaat hechten.”
5/ Natlakken
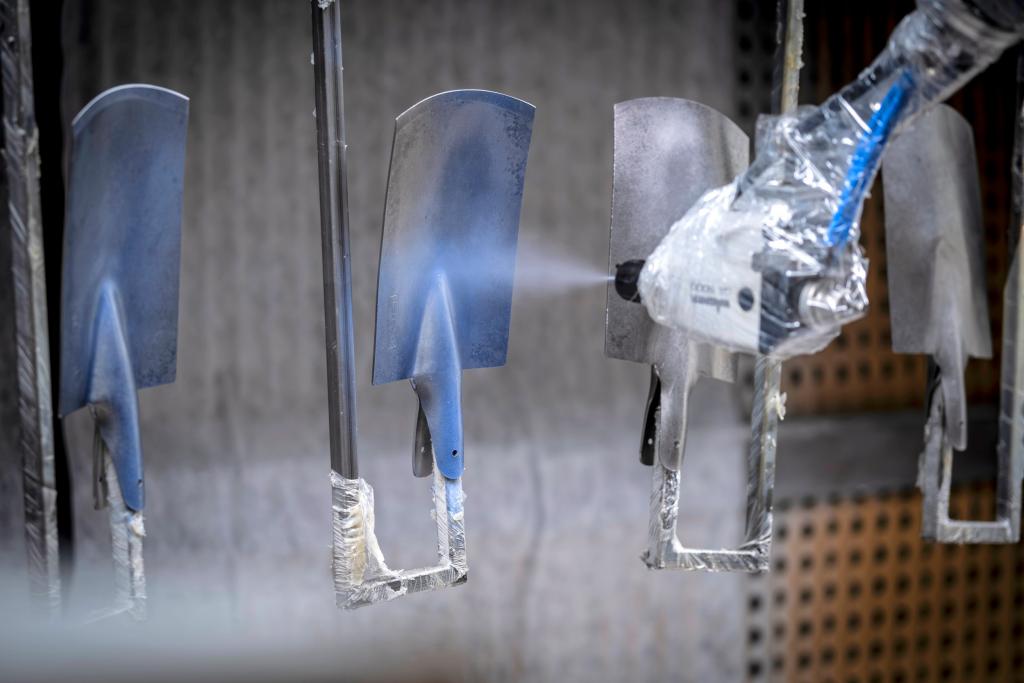
Een spuitrobot brengt aan de hand van statische elektriciteit een dunne laklaag aan op het spadeblad. Dit heeft vooral een esthetische functie, stelt Temmerman: “Het voorkomt dat de spades door de luchtvochtigheid zouden roesten in de winkel. Maar zodra de spade in gebruik is, willen we dat die laklaag zo snel mogelijk verdwijnt. De lak is immers minder hard en glad dan het onderliggende staal. Een solventlak zou de makkelijkste keuze zijn, maar we kiezen bewust voor een natlak op waterbasis. Dat is beter voor het milieu en het is ook gezonder voor onze productiemedewerkers.”
6/ Houten steel
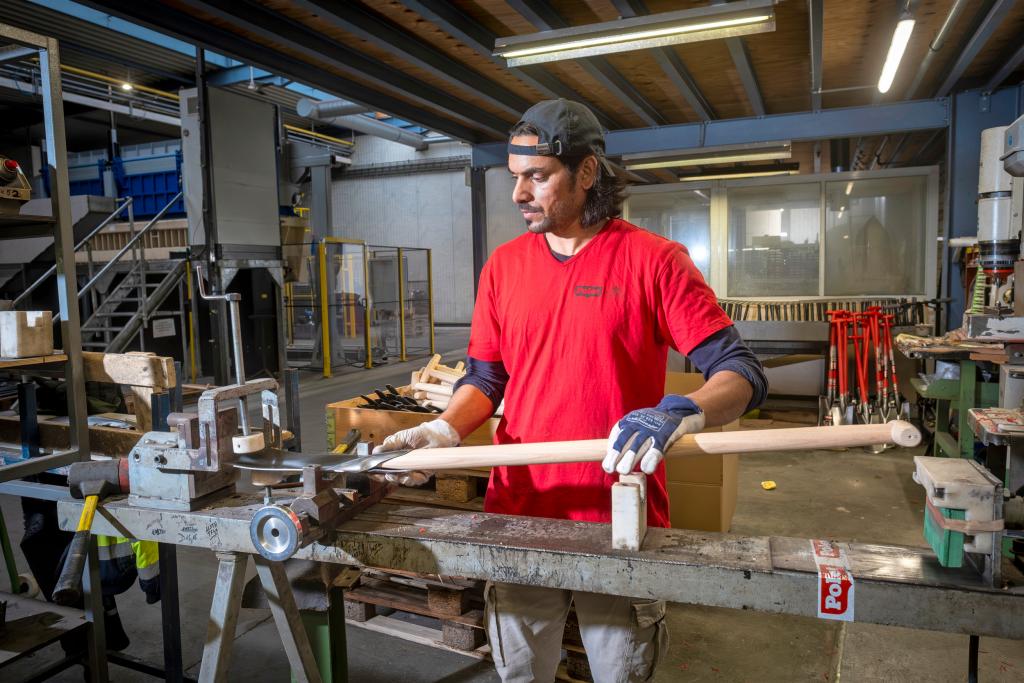
De meeste spades van Polet-De Pypere krijgen een steel in essenhout. “Een houtsoort die ook weer kwaliteiten als taaiheid en rekbaarheid combineert”, stelt Stijn Temmerman. “Beuk is harder, maar is daardoor ook brozer en zal dus sneller breken.” De steel van de spade wordt met grote kracht door middel van perslucht in de leest geduwd. Met een of twee klinknagels hamert een operator de steel helemaal vast.