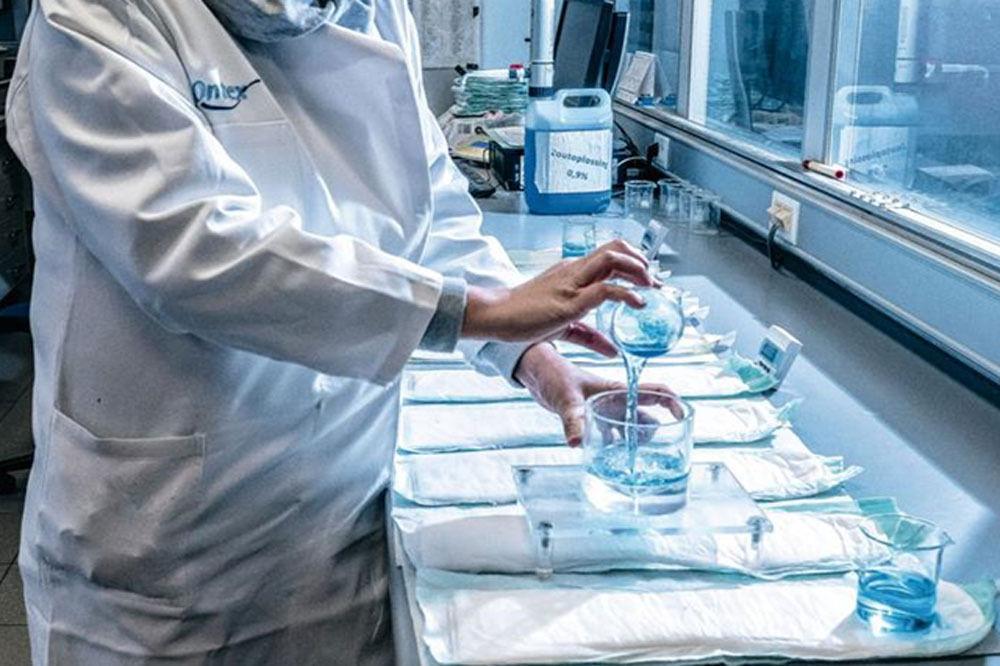
Bij Ontex zijn comfort en duurzaamheid de twee grote aandachtspunten bij de ontwikkeling van de babyluiers. Plantmanager Jef Monballyu: “De luiers moeten dun en zacht, maar tegelijk ook heel absorberend zijn. En ze moeten goed beschermen tegen lekken.” De onderzoeksafdeling levert een belangrijke bijdrage aan de duurzaamheidsdoelstellingen van Ontex. “In de voorbije vijf jaar zijn we erin geslaagd het grondstoffengebruik voor onze babyluiers met 15 procent terug te dringen”, zegt Monballyu.
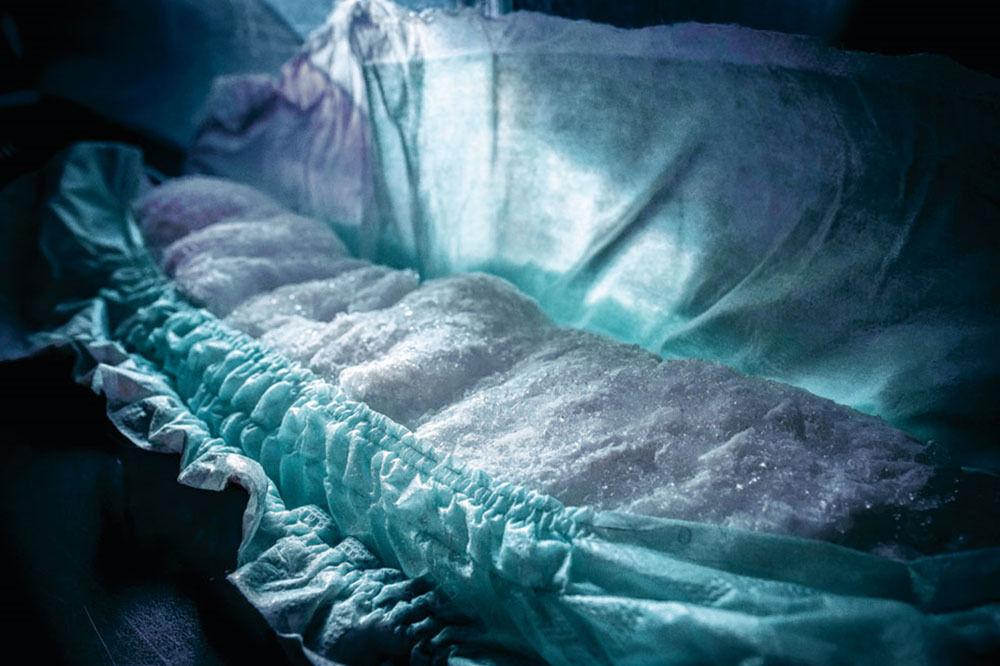
Gemalen papier is de belangrijkste grondstof voor de luiers. Het komt samen met polycarbonaatpoeder in de absorberende kern van de luier. “Dat poeder heeft een heel grote absorptiecapaciteit, tot 33 keer het eigen gewicht”, legt Jef Monballyu uit. “Ter vergelijking: het gemalen papier neemt zeven keer zijn eigen gewicht in water op.” Voor de zijkanten, de opstaande randjes en de verbindingsstukken puzzelt Ontex met kunststoffen die ofwel veel vocht opnemen (hydrofiel), ofwel vocht afstoten (hydrofoob).
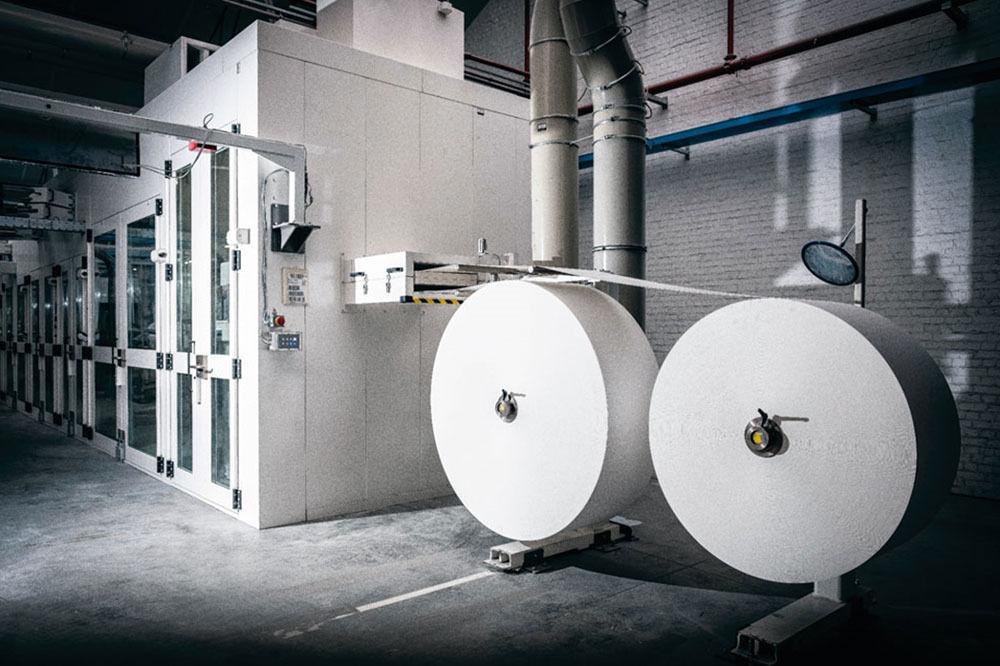
De eerste echte stap in de productie is het malen van de papiervellen. De snel ronddraaiende hamers van de hamermolen vermalen het papier tot een soort watten. Na het toevoegen van het superabsorberende poeder is de grondstof voor de absorberende kern klaar.
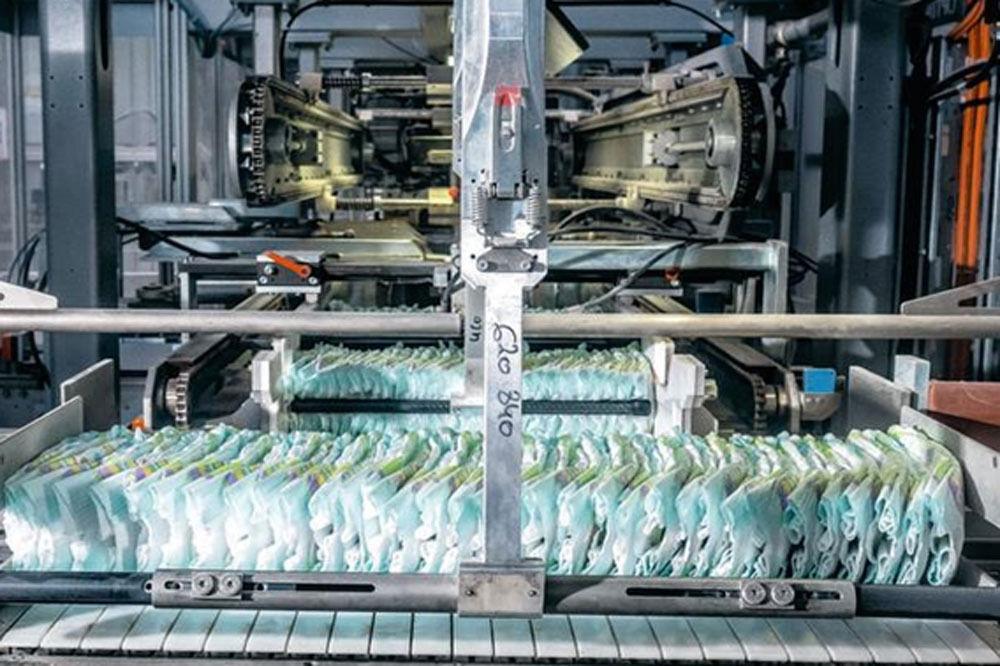
Rond de absorberende kern moet een luier worden gebouwd. Dat gebeurt in een volautomatische productielijn die de verbindingsstukken en de laagjes van de broekjes in de juiste maten en vormen snijdt, die plooit en aan elkaar lijmt. Tijdens het hele productieproces is er voortdurende cameracontrole. De gefotografeerde onderdelen en luiers worden vergeleken met een sjabloon. Als er een afwijking is, wordt het broekje of het onderdeel gedetecteerd en automatisch uit de lijn geworpen. Per minuut komen ongeveer 650 luiers van de productielijn.
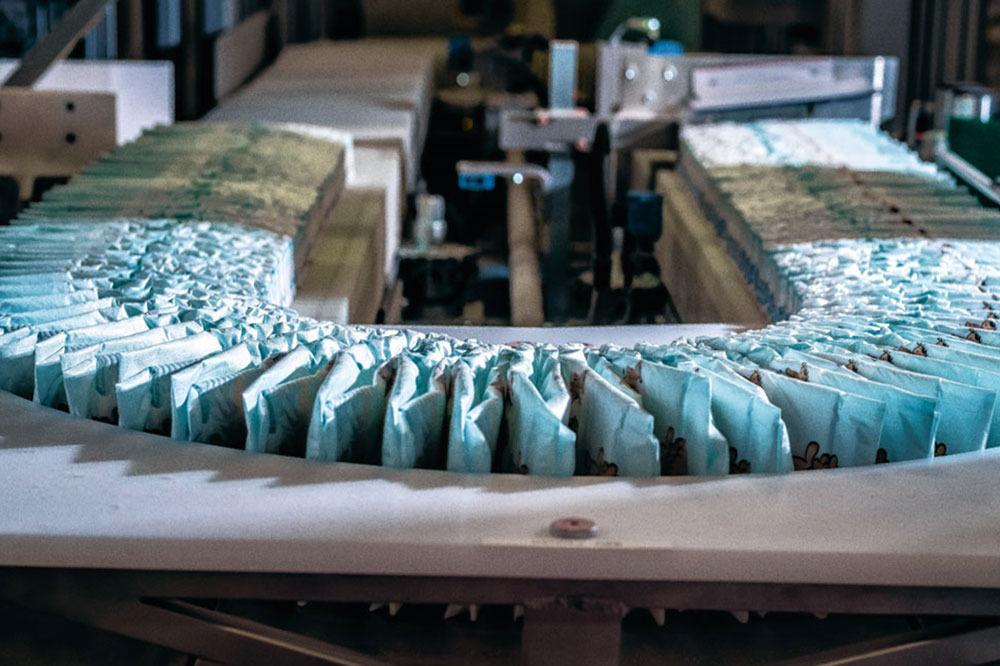
Voor het verpakken passeren de luiers nog langs de comprimeermachine, die ze met een druk tussen 2,5 en 5 ton samenperst, zodat ze minder volume innemen. Alle luiers worden tweevoudig verpakt – eerst in een zak, vervolgens in een doos. De robots zetten de dozen in de juiste configuratie op een pallet, die automatisch naar de foliewikkelaar wordt getransporteerd.
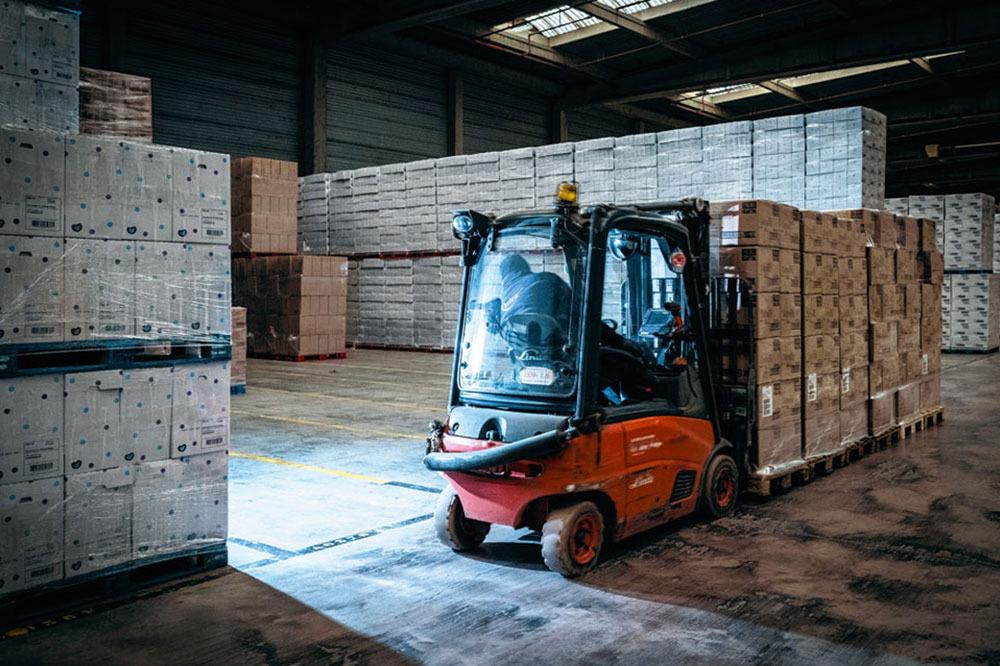
In de magazijnen in Eeklo is plaats voor 15.000 paletten, maar Ontex stockeert een veelvoud in externe magazijnen. Op jaarbasis laadt Ontex in Eeklo 10.000 vrachtwagens met afgewerkte producten.