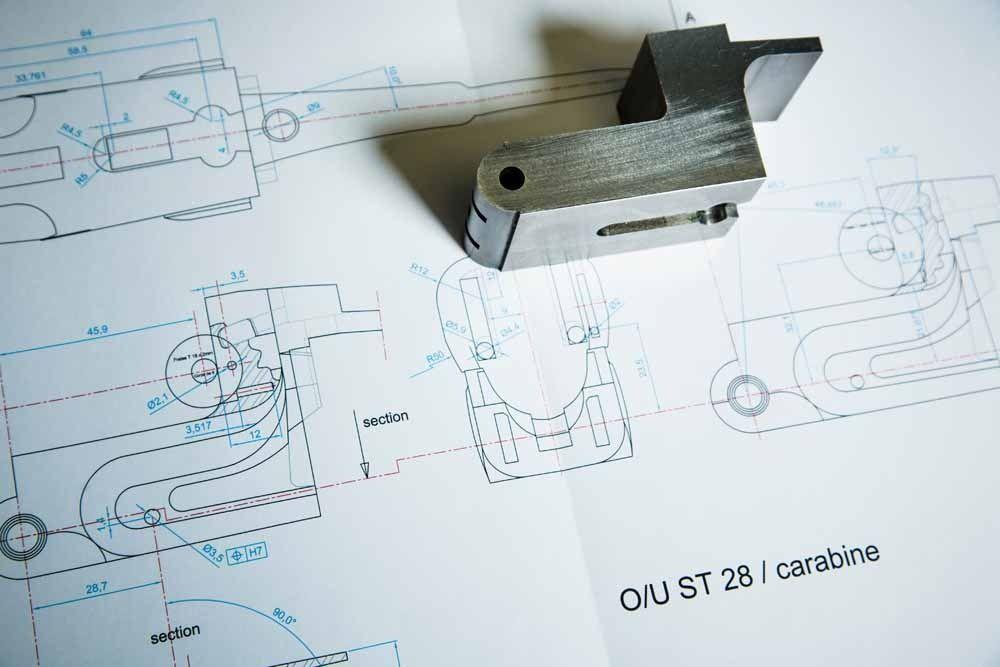
Het ontwerp van de geweren is in al die jaren hetzelfde gebleven. “Op enkele aanpassingen na zijn de plannen nauwelijks veranderd. We hebben ze enkel gedigitaliseerd”, zegt Jean-Marc Stevaux, de meesterknecht van Lebeau-Courally. Elk wapen is uniek en aangepast aan de klant. Die kan niet alleen het kaliber kiezen, maar ook het aantal lopen, de schikking en de afwerking.
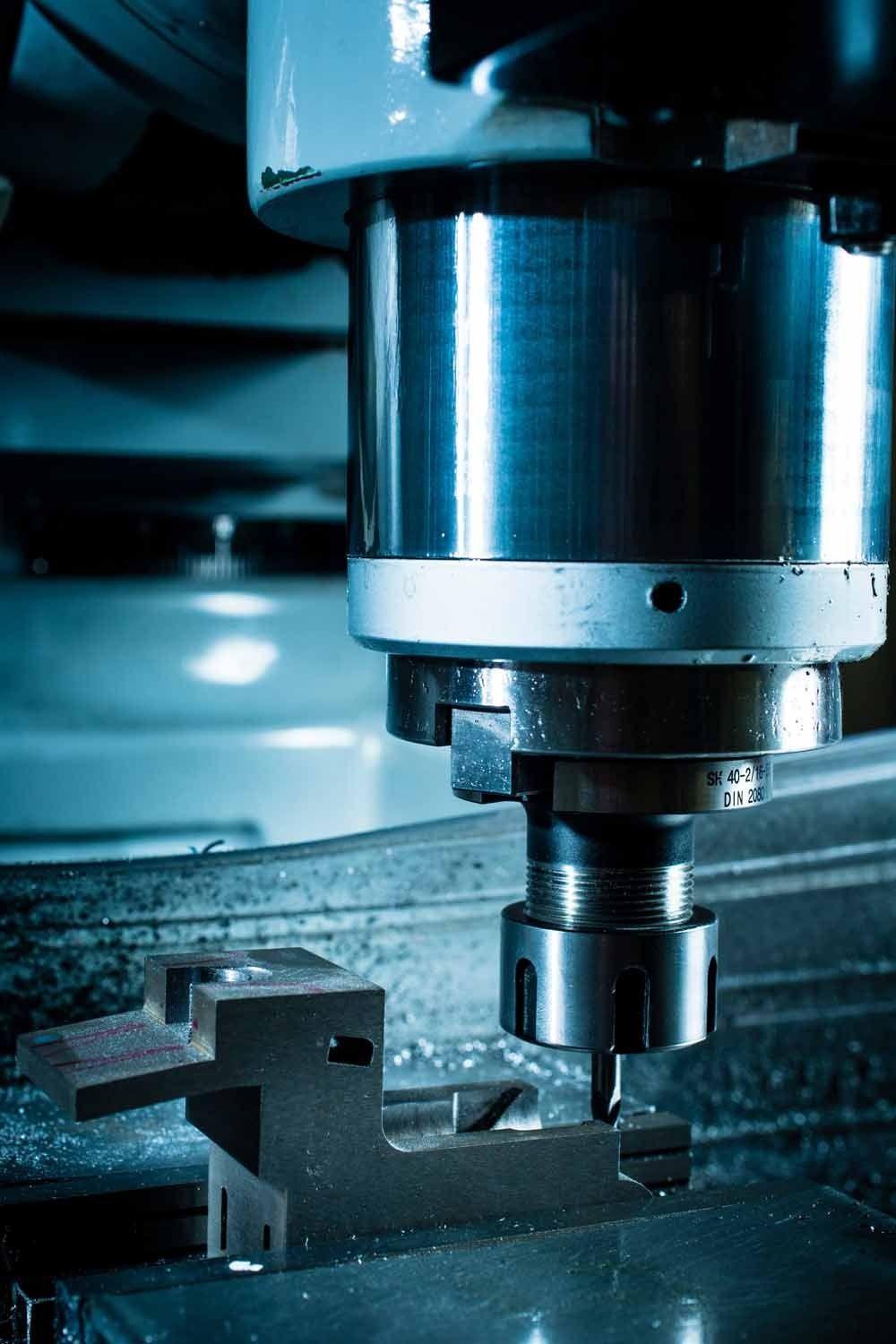
Behalve de lopen en de veren worden alle onderdelen in het bedrijf gefabriceerd. Uit stukken staal en met behulp van twee machines maakt het bedrijf er ruim honderd onderdelen. “Onze vraag is dermate specifiek dat het moeilijk zou zijn toeleveranciers te vinden die bereid zijn voor ons slechts een handvol zeer karakteristieke onderdelen te maken”, zegt Stevaux.
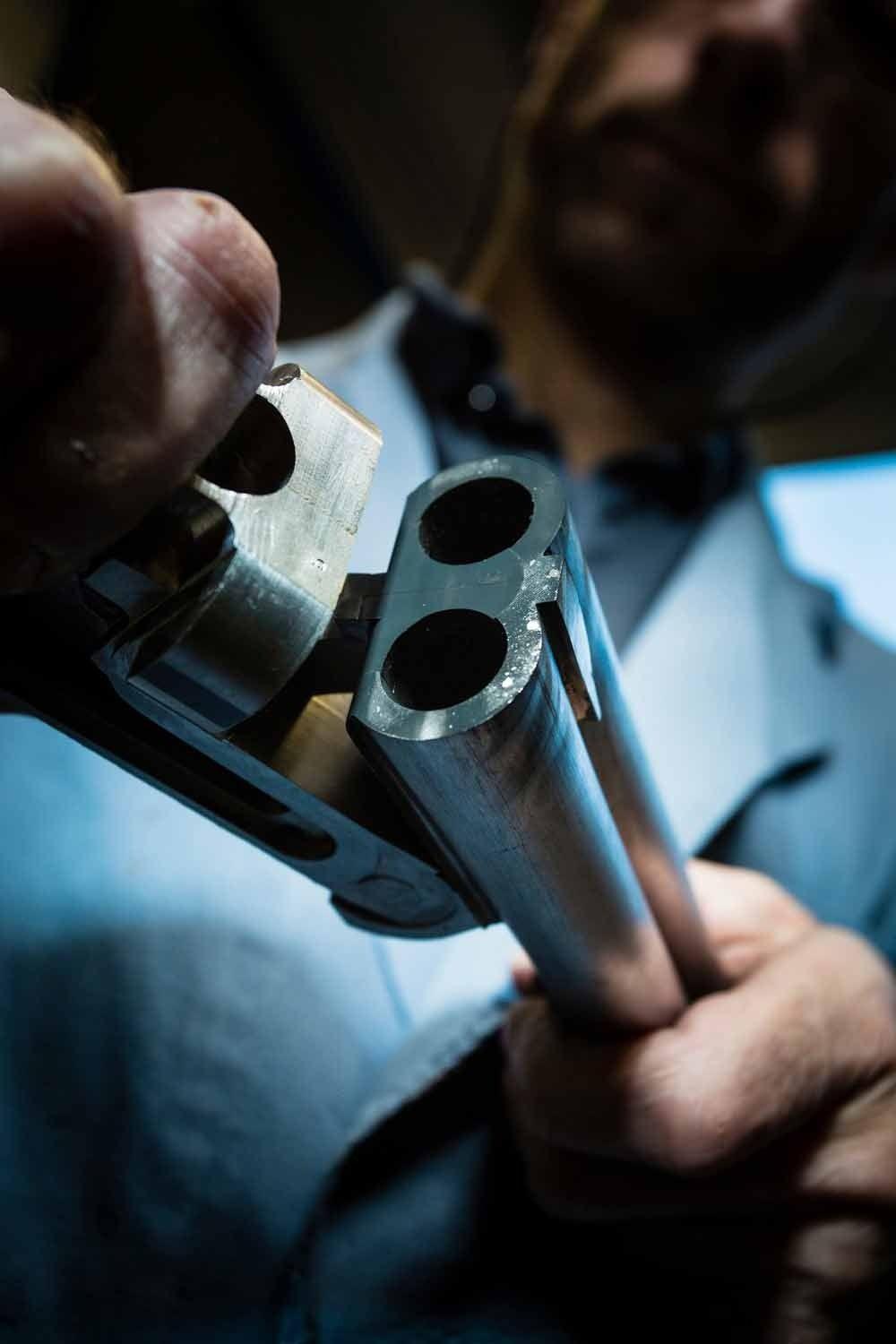
De lopen worden niet in de fabriek vervaardigd, maar komen in onbewerkte toestand aan. Ze worden gesoldeerd, een lastechniek die gebruikmaakt van een drager in metaal die wordt verhit tot vloeibare toestand. Een precisiewerkje dat niet alleen de esthetiek van het wapen ten goede komt, maar het ook mogelijk maakt de richtbalk net boven de lopen af te stellen.
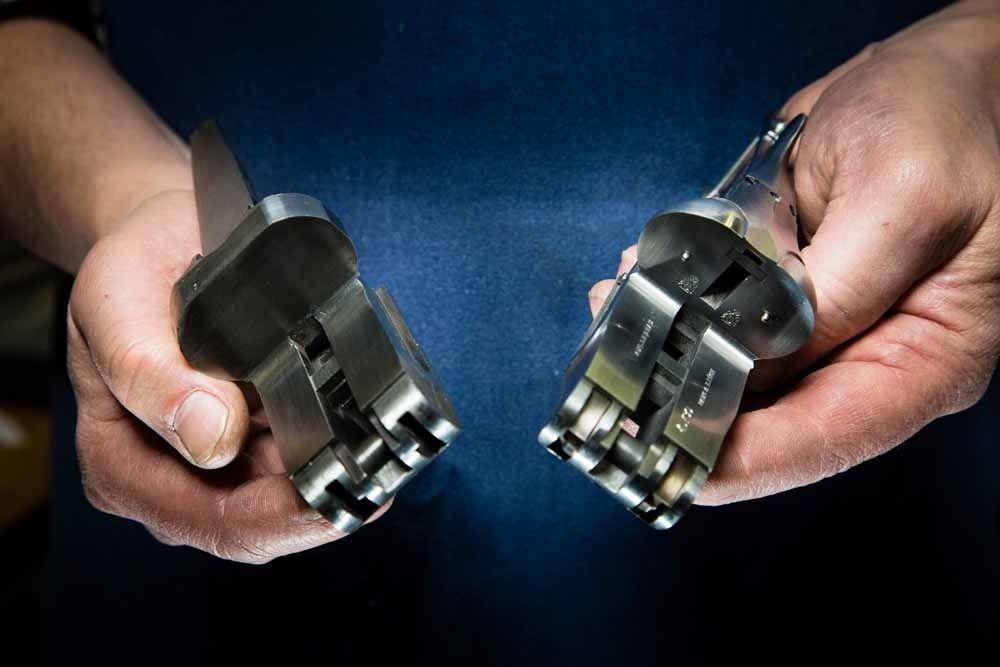
De onderdelen worden met de hand geassembleerd. Eerst worden de drie belangrijkste onderdelen geassembleerd. Dat zijn de lopen, het voorhout waarop de lopen rusten en de bascule. Dat deel bevat het trekker- en openingsmechanisme. De assemblage gebeurt met behulp van roetzwart. Het uiteinde van de lopen wordt met een vlam zwartgemaakt en wanneer ze met de bascule worden verbonden, laten ze daar een afdruk achter die fungeert als referentiepunt voor latere retouches. Als die ‘basculage’ klaar is, wordt de rest van het mechanisme toegevoegd.
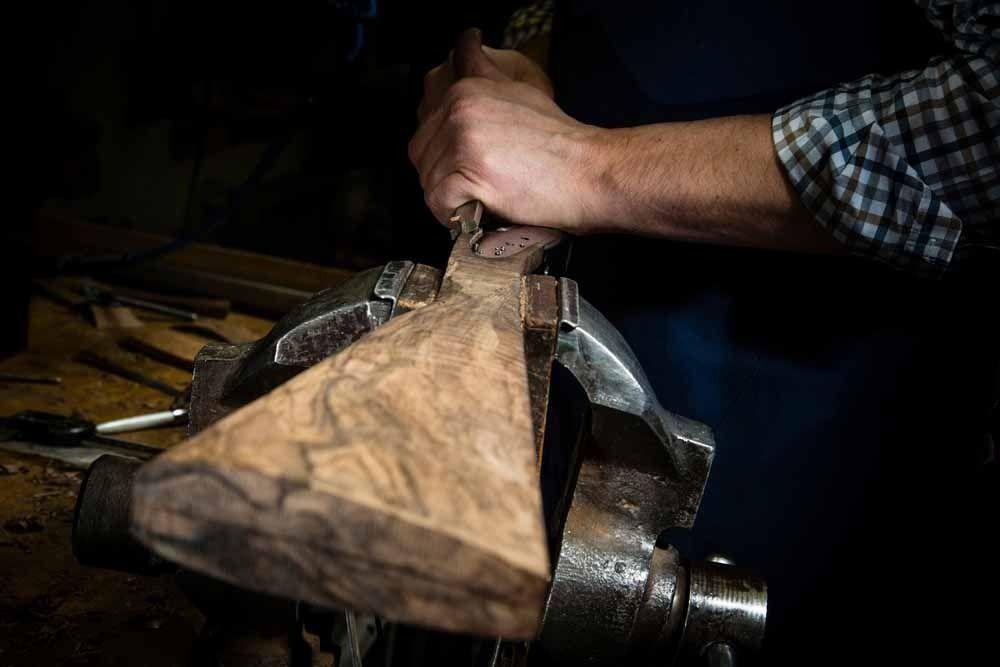
De kolf van het geweer wordt uitgevoerd in notenhout. “We gebruiken dat in de eerste plaats omdat het mooi is, maar notenhout heeft nog voordelen. Het is een soepele houtsoort die niet barst”, licht de meesterknecht toe. “Elke kolf is uniek en wordt aan zijn toekomstige eigenaar aangepast. “Niet enkel of die links- dan wel rechtshandig is, maar ook zijn grootte is belangrijk. Net zoals een kleermaker nemen we bij de bestelling dus de maten van de klant op”, zegt nog Jean-Marc Stevaux. De kolf wordt op maat gesneden en op het mechanisme van het geweer geschroefd.
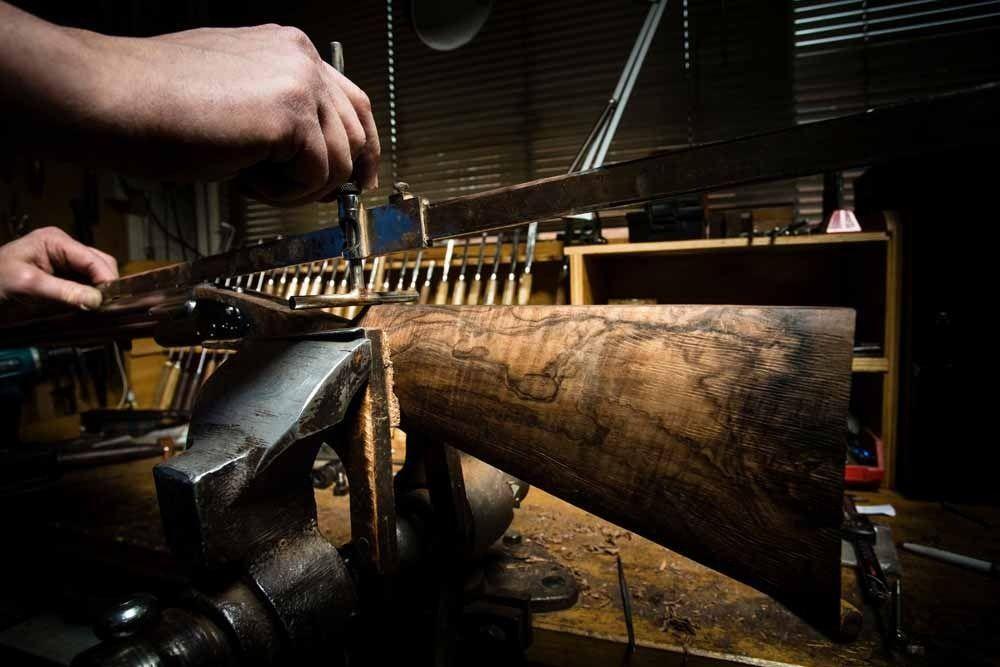
Nu het wapen ruwweg klaar is, wordt het opnieuw volledig gedemonteerd om bepaalde onderdelen nog een laatste keer precies af te stellen. Vooral met het oog op de esthetiek, hoeken worden bijvoorbeeld afgerond. “Voor sommige onderdelen doen we dat nog met de beitel, maar een groot deel gebeurt machinaal”, zegt de meesterknecht. Vervolgens gaat het geweer naar de proefbank voor vuurwapens in Luik. Die garandeert dat het wapen conform is en werkt zoals het moet.
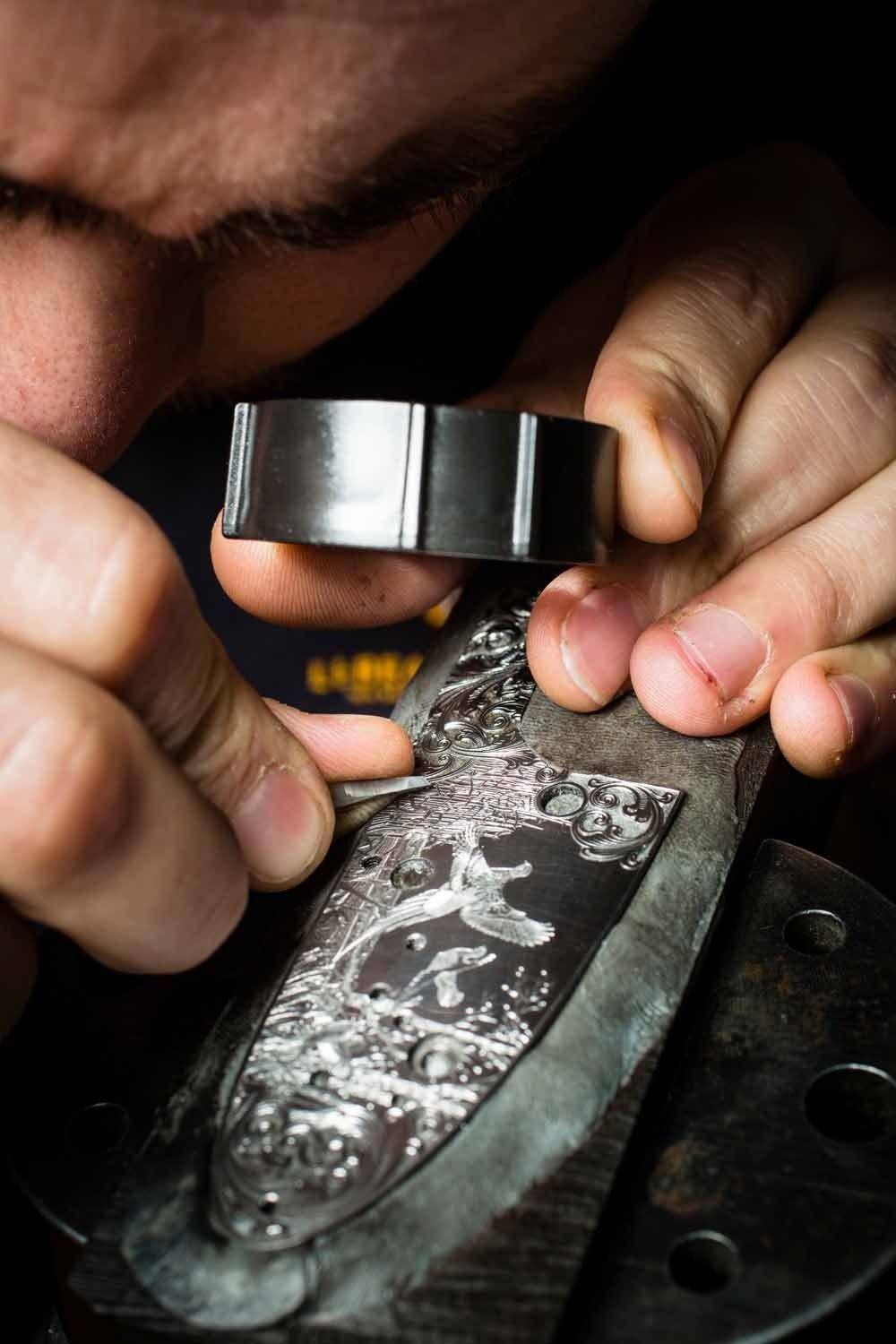
Het geweer moet nu alleen nog een persoonlijk accent krijgen. Een van de meest tijdrovende fases van het productieproces. “Naargelang de complexiteit van de tekening moet je rekenen op een tot drie maanden werk”, zegt de graveur. In speciale bestellingen kruipt soms nog veel meer tijd. Zo wenste een niet nader genoemde politicus dat er op zijn wapen een reproductie van een beroemd schilderij werd gegraveerd. Het duurde vijf jaar eer de graveur daarmee klaar was.