Aan de rand van Eindhoven staat een merkwaardig huis. Het is de eerste woning ter wereld op de privémarkt die volledig uit 3D-geprint beton is opgetrokken. Dat kon dankzij de expertise van Weber Beamix, een onderdeel van de Franse bouwmaterialenproducent Saint-Gobain. De techniek is duurzamer dan klassiek bouwen. “Een heerlijk huis”, zeggen de bewoners.
Sinds augustus wonen Elize Lutz en Harrie Dekkers in een huis van het project Milestone in het Nederlandse Eindhoven. Het is het eerste residentiële project ter wereld dat volledig uit 3D-geprint beton is opgetrokken. De productie gebeurde in een fabriekshal in Eindhoven, waar Weber Beamix, een onderdeel van de Franse bouwmaterialenproducent Saint-Gobain, de eerste industriële 3D-betonprintfabriek in Europa doet draaien. “Onze eerste doelstelling was duurzaamheid”, aldus projectleider Gian Sterken. De bouwsector is verantwoordelijk voor 11 procent van de CO2-uitstoot. Sterken schat dat Weber Beamix de klimaatvoetafdruk van een huis met de 3D-productie met 40 tot 60 procent kan beperken. Het bedrijf werkt ook aan CO2-neutraal beton.
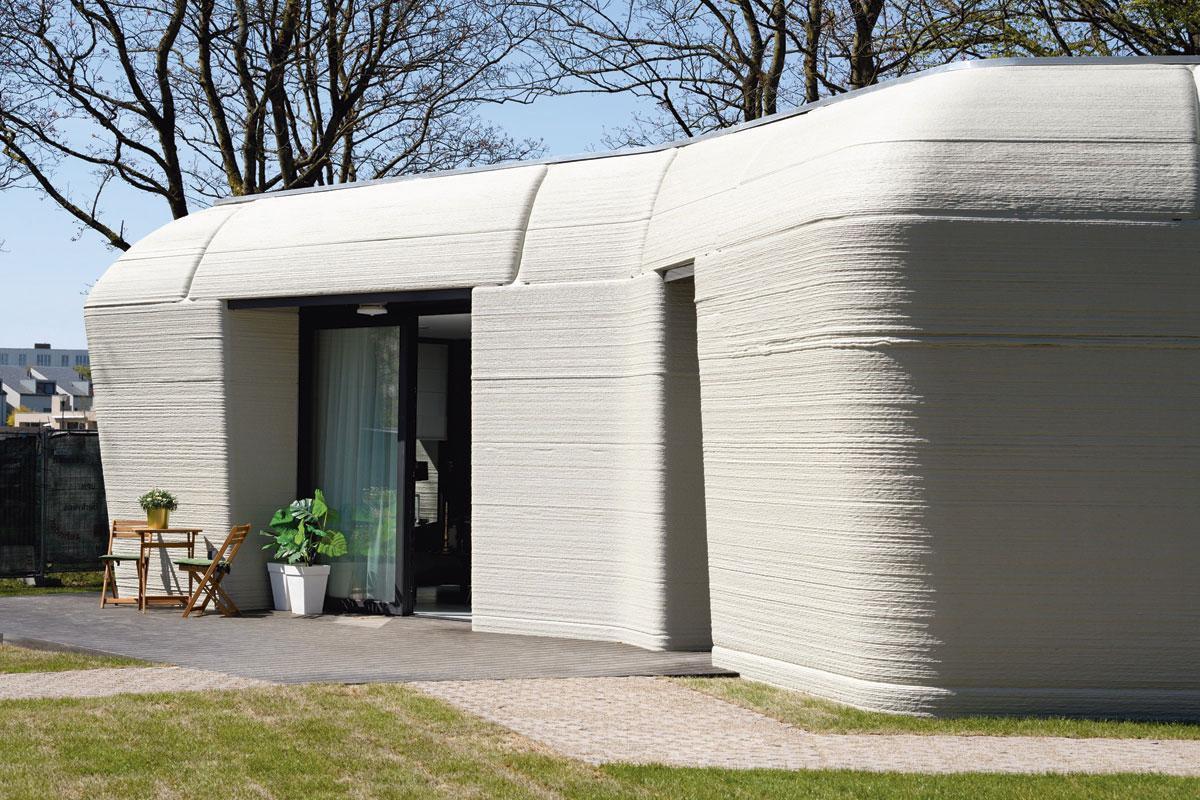
Geen staal of extra beton
Bij een klassieke constructie wordt beton in een kist gegoten. Dat veroorzaakt veel afval. In de Eindhovense fabriekshal spuit een 3D-printrobot laag per laag een betonnen constructie, bijna zoals tandpasta uit een tube komt. Dat gebeurt onder toezicht van twee personen. Kisten en ander klassiek bouwmateriaal zijn overbodig. Met de technologie kunnen holle, bolle of ronde structuren worden gemaakt, en het beton kan veel exacter, en dus efficiënter en duurzamer worden benut. Het holle bouwmateriaal wordt onder spanning gezet en is even sterk als volledige betonblokken, maar met veel minder cement. Het materiaal kan heel de structuur van het huis dragen. Sterken: “Wij zijn de enige 3D-producent die geen extra beton of staal hoeft te gebruiken om het huis stabiel te houden of het dak te schragen. Nog een besparing op materiaal dus.”
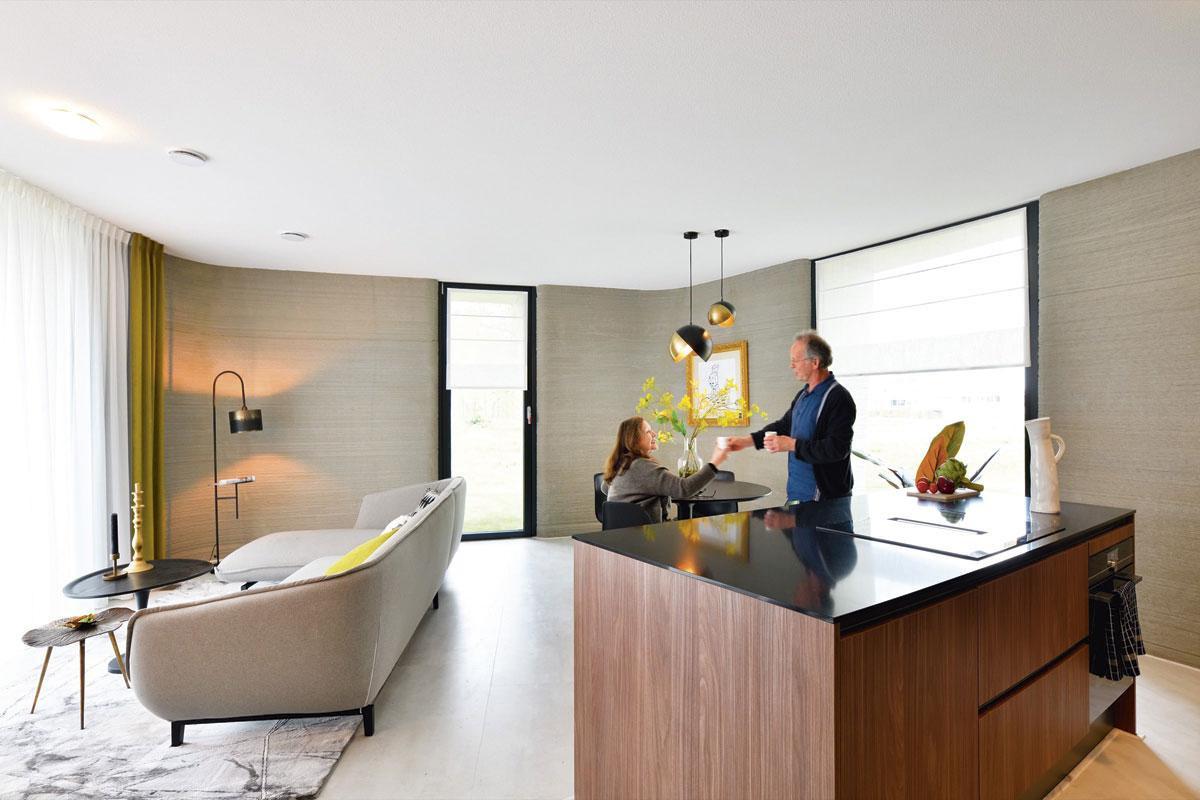
In de fabriekshal in Eindhoven liggen ook tuinmeubilair en fietsbruggen klaar voor transport. De 3D-productie in de fabriek is geschikt voor onderdelen tot 12 meter lang. Voor het huis in Eindhoven moesten 24 onderdelen worden geprint. Dat nam 118 uur in beslag. De plaatsing van de woning duurde een dag. Door het huis in de fabriek te creëren bespaart het bedrijf ook op personeels- en materiaalvervoer naar de werf.
Uit de fouten bij het optrekken van de eerste woning, zoals barsten in een muur en logistieke problemen, werden conclusies getrokken voor de andere vier die voor Milestone gebouwd moeten worden. “Die barsten zijn geen probleem en hebben geen enkele invloed op de stabiliteit”, sust Jelle Houben, wiens kantoor Houben/Van Mierlo Architecten het ontwerp van Milestone tekende. Voor het ontwerp van het eerste huis maakte hij maximaal gebruik van de architectonische ruimte die 3D-productie biedt. Tijdens het bouwproces moest de architect echter toegevingen doen. Het dak werd bijvoorbeeld afgevlakt. Houben: “Bij het ontwerp van de volgende huizen kunnen we rekening houden met de opgedane ervaring om de architecturale meerwaarde van 3D-printing ten volle te benutten.”
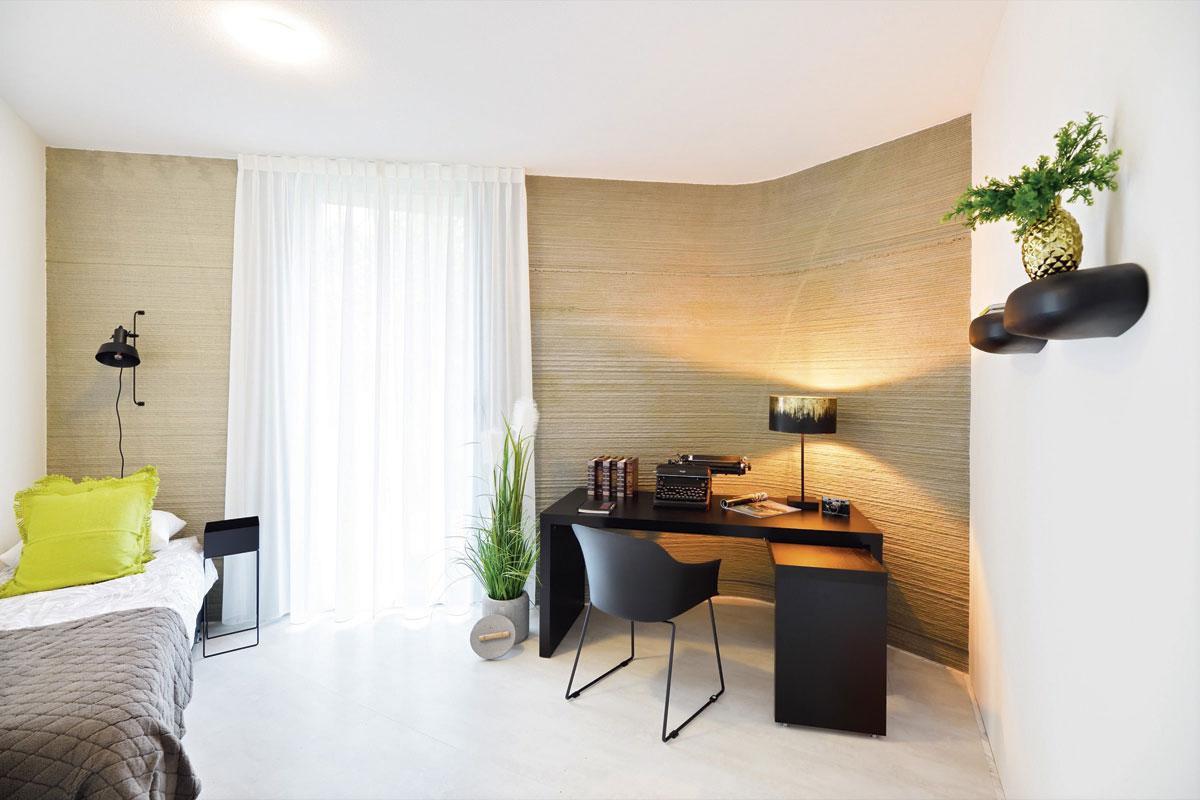
Het ideale moment
De Technische Universiteit Eindhoven is een van de partners van het Milestone-project. “3D-betonproductie bestaat al twintig jaar”, zegt decaan bouwkunde Theo Salet. “Steeds meer universiteiten en ondernemingen zijn ermee bezig. Toch staat de technologie nog in haar kinderschoenen. Weinig bedrijven wilden het risico nemen. Maar nu beleven we een kantelmoment. De Nederlandse bouwgroep Van Wijnen, die Milestone bouwt, engageerde zich om belangrijke investeringen in 3D-betonprinting te doen. Andere grote Nederlandse sectorgenoten volgen.”
Ook grote betonproducenten zoals Heidelberger en Holcim zetten volop in op 3D-productie, weet Hervé Camerlynck, de directeur van de Federatie van de Belgische Cementnijverheid. “Voorlopig blijft 3D-betonprinting beperkt tot gedetailleerd maatwerk. Ik verwacht dat de bouwsector op termijn met één softwarepakket seriewoningen kan afleveren tegen een prijs die concurreert met die van de klassieke bouw.”
Salet bevestigt dat 3D de industrialisering van de bouwsector zal aansturen. “Maar een 3D-fabriek zal nooit rijhuizen aan de lopende band uitspuwen. De digitalisering maakt het mogelijk te werken met standaardsoftware, die kan worden aangepast om huizen op maat af te leveren. 3D-betonbouw verloopt twee keer sneller dan de klassieke bouwmethode. Omdat het bouwproces centraal wordt aangestuurd, kan de logistieke winst het tempo nog sterker versnellen. De techniek komt op het ideale moment. Nederland heeft 1 miljoen nieuwe en duurzame woningen nodig. Industriële 3D-betonproductie kan die leveren en betaalbaar houden.”
Ook in de Verenigde Staten worden met die techniek de eerste commerciële bouwprojecten ontwikkeld. Het aannemingsbedrijf Icon plant zo honderd woningen in Texas. Het gebruikte die techniek al voor woningen in non-profitprojecten in Austin en Mexico. Icon hoopt de huizen te verkopen tegen de helft van de huidige marktprijs.
Het is wel nog goedkoper om klassiek te bouwen. “De ontwikkeling en het opstartrisico wegen nog zwaar in de kostprijs van de eerste woningen”, weet Sterken. “De bouw van de tweede fase van Milestone is commercieel al interessanter.” Eindhoven is het kenniscentrum van Saint-Gobain voor de rest van Europa. Door schaalgrootte hoopt de groep 3D-printing te rendabiliseren.
Vlaamse markt
Weber Beamix werkt ook voor de Vlaamse markt. Het produceerde de zwembadwanden die Groep Van Roey plaatste in Sportoase Groot Schijn in Deurne, die eind september 2021 de deuren opende. “Dit is de eerste commerciële toepassing van 3D-printing in de Belgische bouwsector”, vertelt Geert Verachtert, directeur strategie en businessdevelopment van de bouwgroep. Groep Van Roey participeert ook in Kamp C, een initiatief van de provincie Antwerpen voor 3D-printing. Kamp C bouwde in Westerlo met de mortel van Beamix een eerste proefwoning met de techniek.
Van Roey werkte voor de wanden met een building information model (BIM). Dat is een digitaal proces dat het ontwerp, de uitvoering en het beheerproces van de 3D-printing en de constructie op de werf begeleidt. “Zo kunnen we veel preciezer werken, waardoor de foutenmarge sterk afneemt”, legt Geert Verachtert uit. “Door de bekistingsstructuur, de afvalstromen en de handarbeid te beperken, werken we ook efficiënter. Bouwen met 3D-printing is voorlopig vooral geschikt voor complexe constructies, zoals de gebogen wanden van het zwembad. Op termijn verwacht ik dat de techniek ook zal worden ingezet voor andere toepassingen, zoals de bouw van woningen. Ik ben ervan overtuigd dat de combinatie van 3D-printing en industriële bouw ooit een oplossing zal zijn voor het gebrek aan betaalbare, kwalitatieve en meer duurzame woningen.”
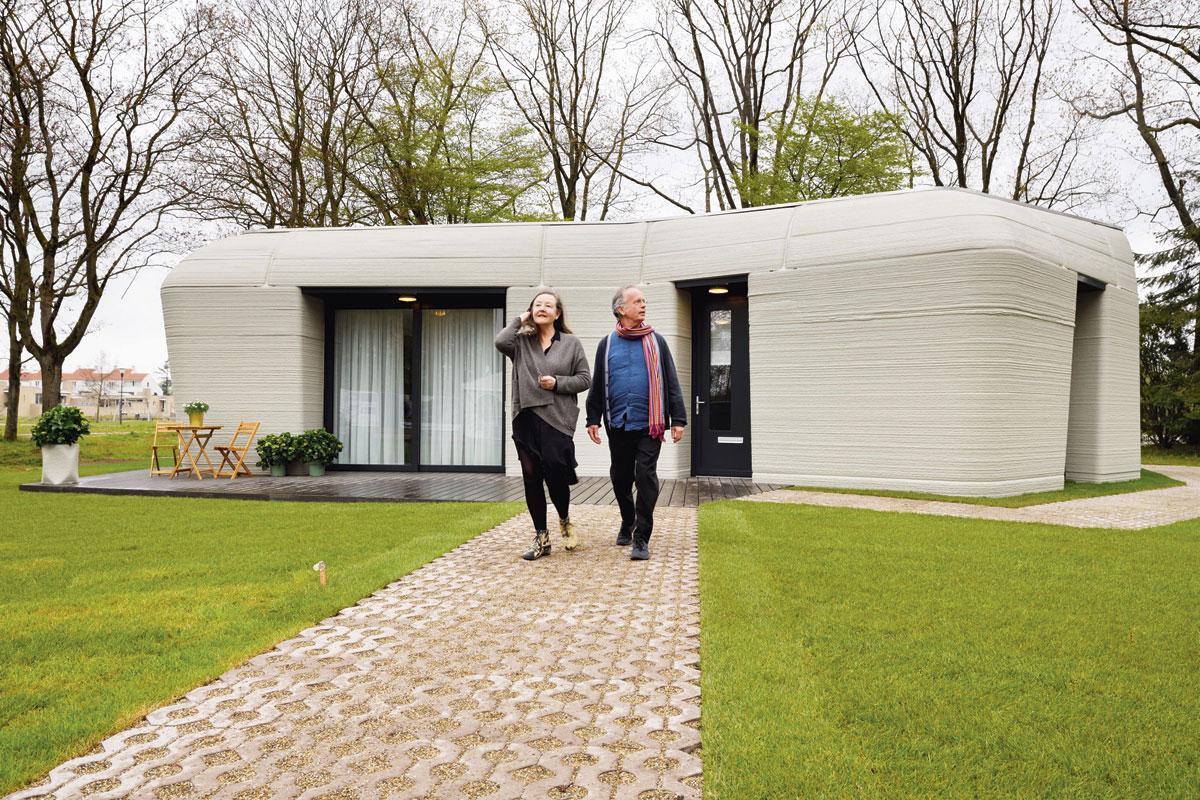
De bewoners van de woning in Eindhoven zijn alleszins tevreden. “Onze woning ziet eruit als een sprookjeshuis in de Efteling en ze helpt bovendien in de strijd tegen de klimaatopwarming”, zegt Elize Lutz. “Kortom: het is een heerlijk huis.”
60 procent bedraagt de maximale beperking van de CO2-uitstoot bij de bouw van 3D-geprint gebouw.