Meer dan twee derde van alle vrachtwagen- trailers op onze Europese wegen heeft een dekzeil dat vervaardigd is bij Sioen. Het spinnen en weven van het technisch textiel vindt plaats in Moeskroen. In de fabriek in Ardooie krijgt het weefsel zijn coating.
Familiebedrijf en multinational
Sioen is een naam als een klok in de Belgische bedrijfswereld. CEO Michèle Sioen werd door Trends verkozen tot Manager van het Jaar 2017. Met vijftig vestigingen in twintig landen en een wereldwijde afzetmarkt mag het West-Vlaamse bedrijf zich een multinational noemen. Tegelijkertijd is Sioen een echt familiebedrijf. In Rumbeke startte Adolf Sioen in 1907 een weverij onder de naam Sioen-Sabbe. In 1960 maakte het bedrijf de overstap van klassiek textiel naar het technisch textiel. In een nieuwe fabriek in Roeselare kwam een eerste coatinglijn voor onder meer de productie van dekzeilen voor vrachtwagens. In 1991 vernielde een brand de fabriek en hoofdzetel in Ardooie. Een zware klap, maar met de investering in een nieuwe fabriek legde Sioen de basis voor de expansie in de tweede helft van de jaren negentig. In 1996 trok het bedrijf naar de beurs. Sioen noteert nog altijd op Euronext Brussels, maar de familie Sioen controleert 65 procent van de aandelen. Sioen stelt wereldwijd 4000 mensen te werk en realiseerde in 2018 een omzet van 507 miljoen euro. Sioen is actief in drie sectoren. Het is de wereldmarktleider in technisch textiel (coating), de Europese marktleider in beschermkledij en een groeiende nichespeler in de productie van fijnchemicaliën.
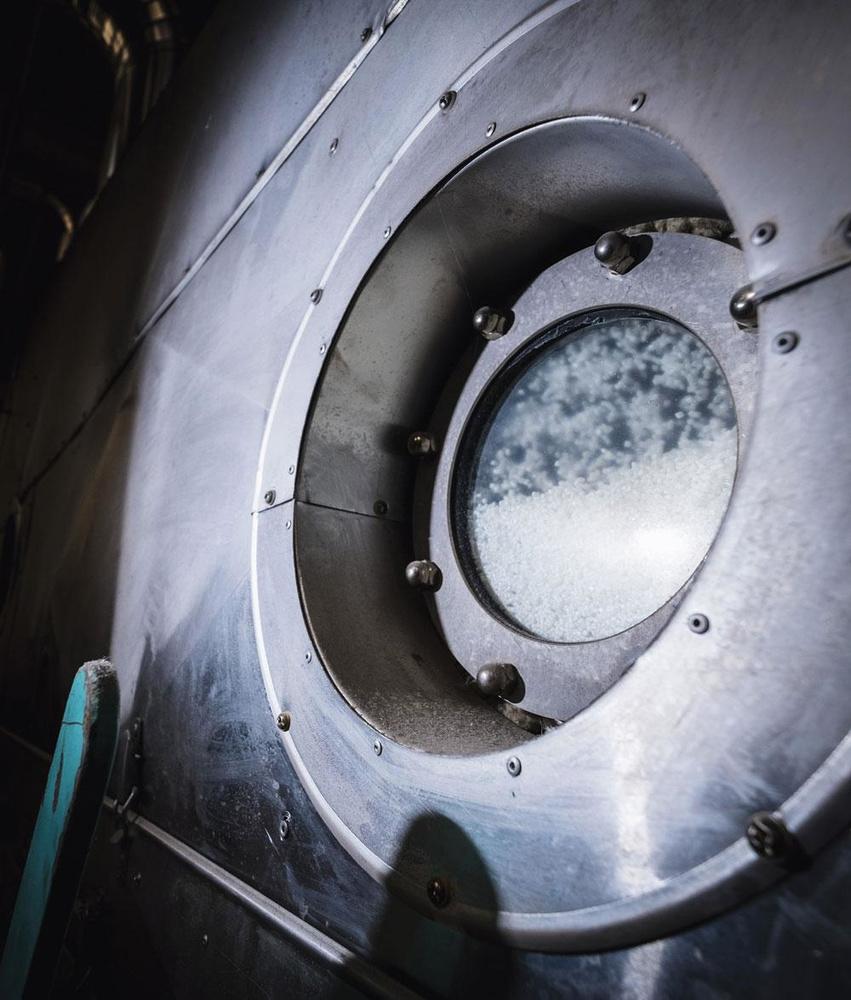
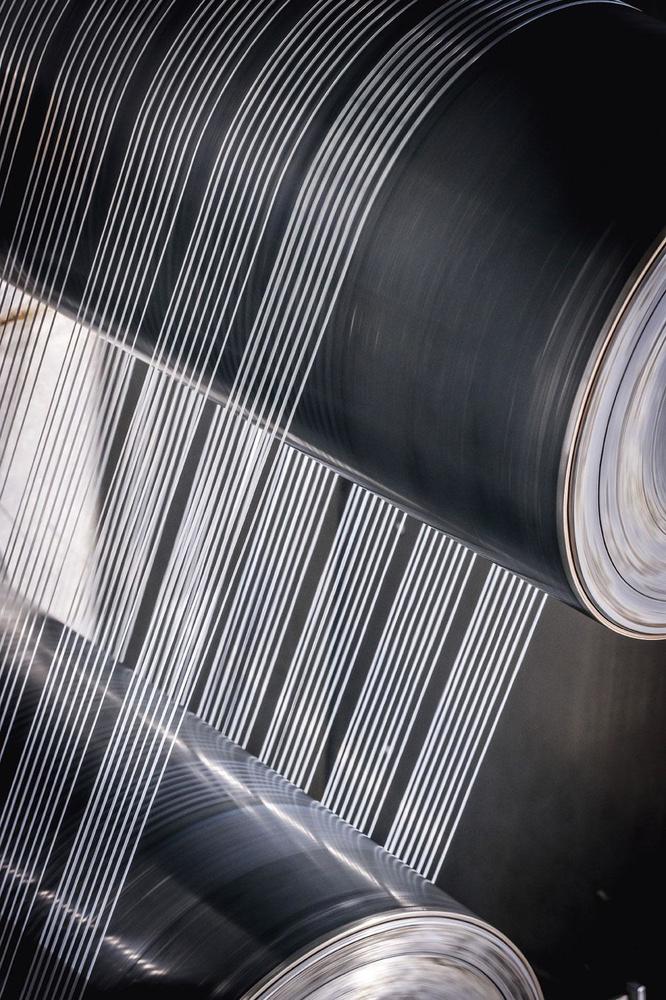
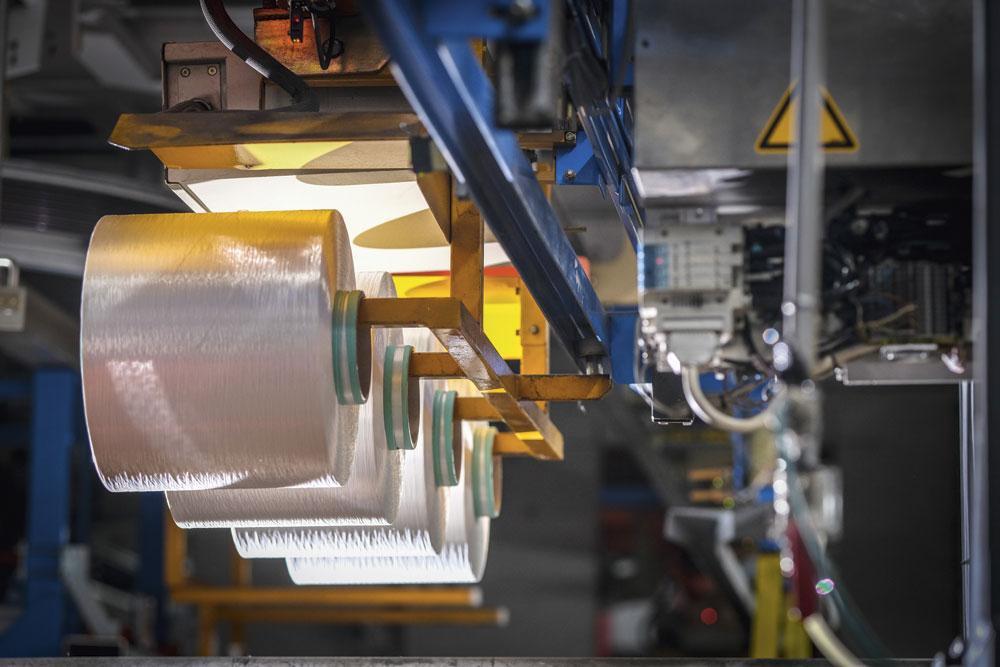
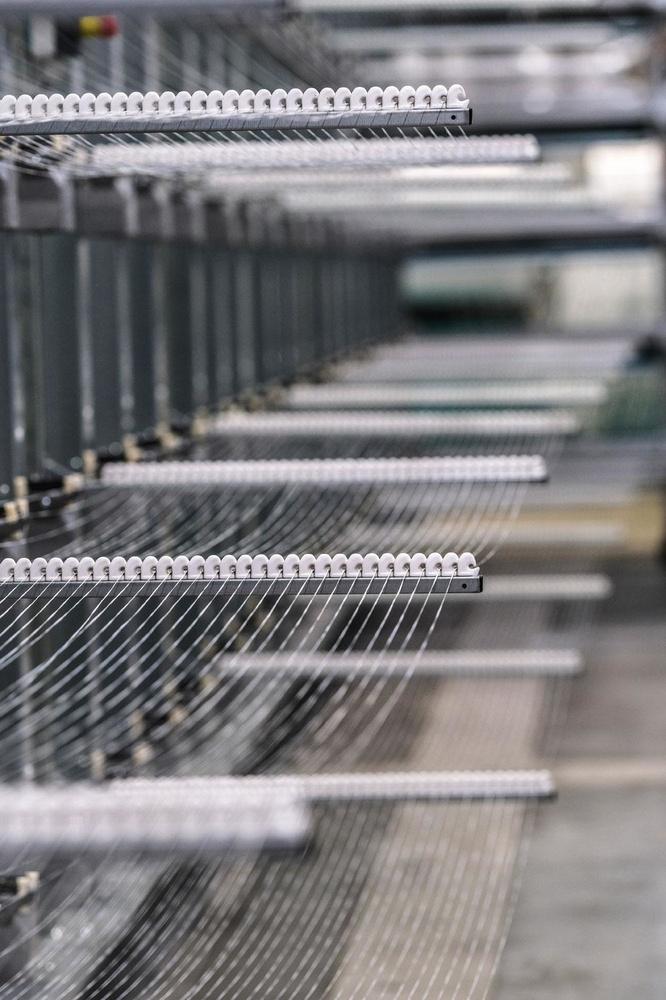
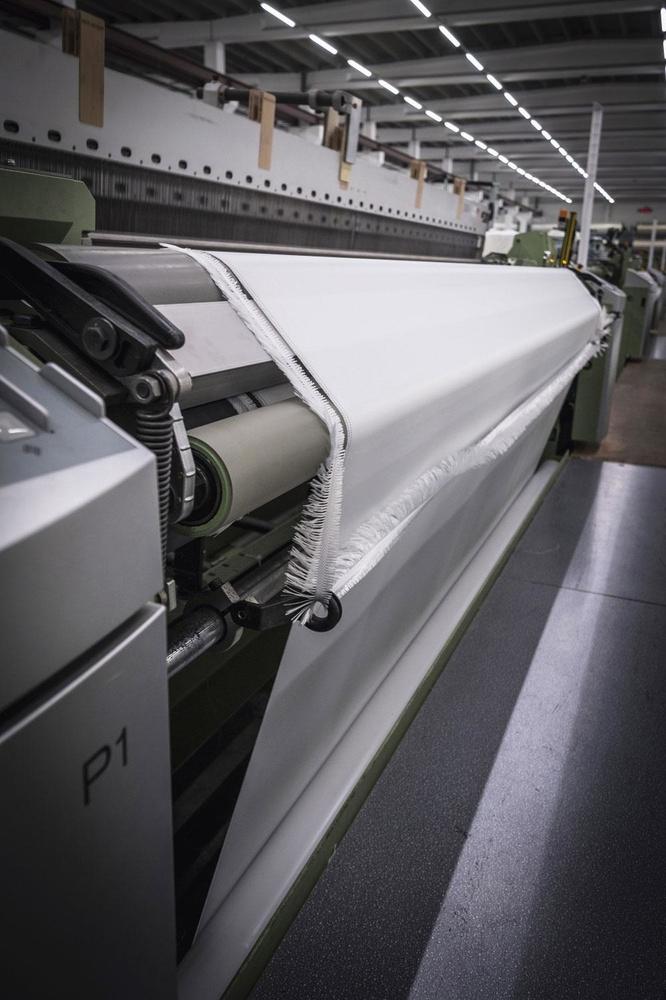
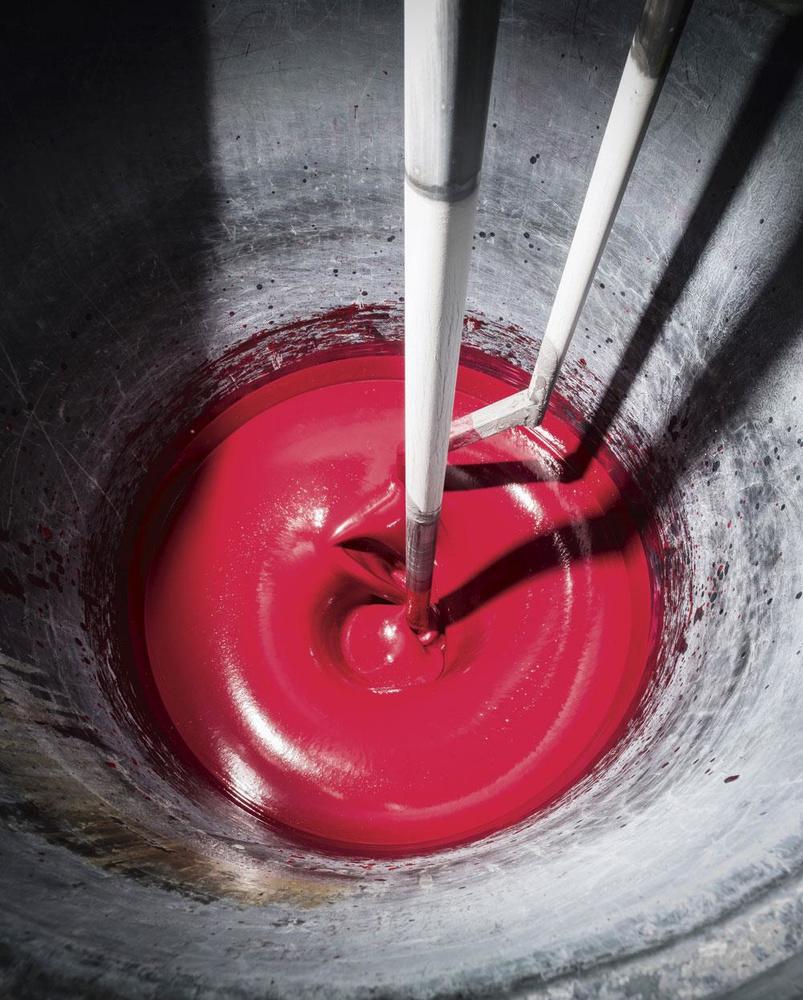
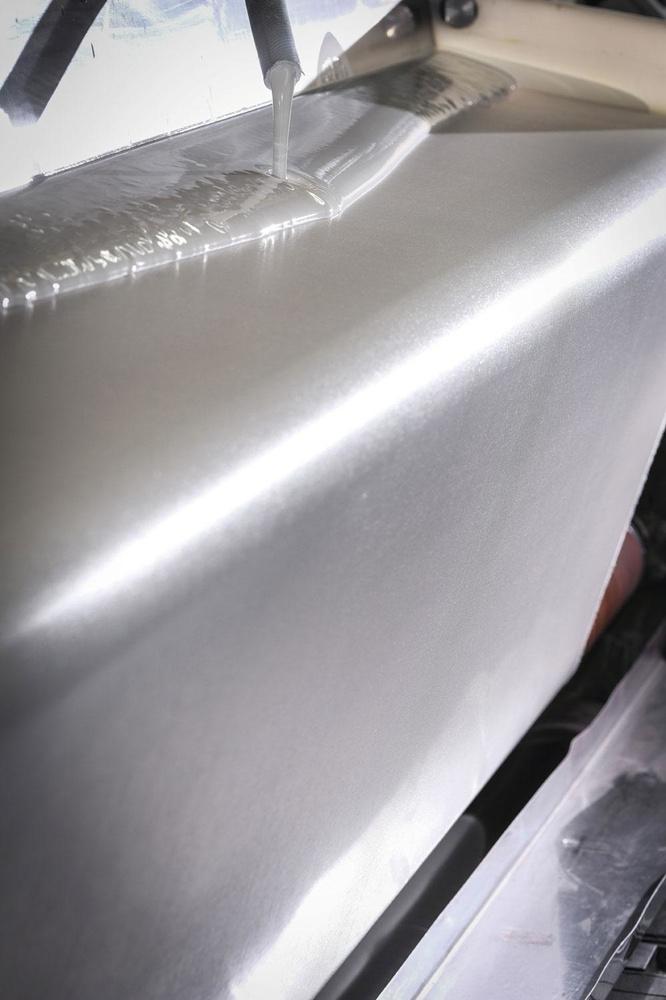
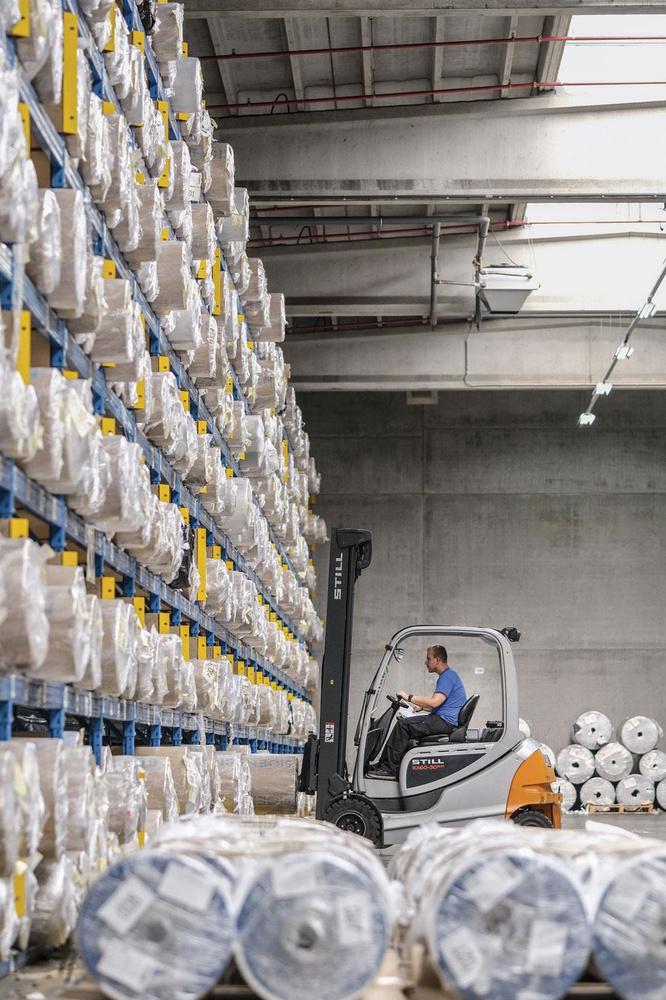